Introduction
Steel gratings are frequently found in underground applications such as stair treads and pipelines, making work easier for operators. They can also be seen as part of drainage water ditches or covers above them due to the combination of bearing bars and crossbars welded together.
That leaves sufficient gaps between each bar, which ensures good ventilation by allowing air to flow freely with no blockages. Many continuous operation ventilators installed at the steel grating vents further intensify this effect, even going so far as to provide a type of fresh air opening for subterranean warehouses.
Underground applications of steel gratings and gratings are not your typical use for the versatile material, but these unique structures could only do their job with it. This article will examine how this metal can be used for more than just walkways in construction sites.
1. What is steel grating for underground applications
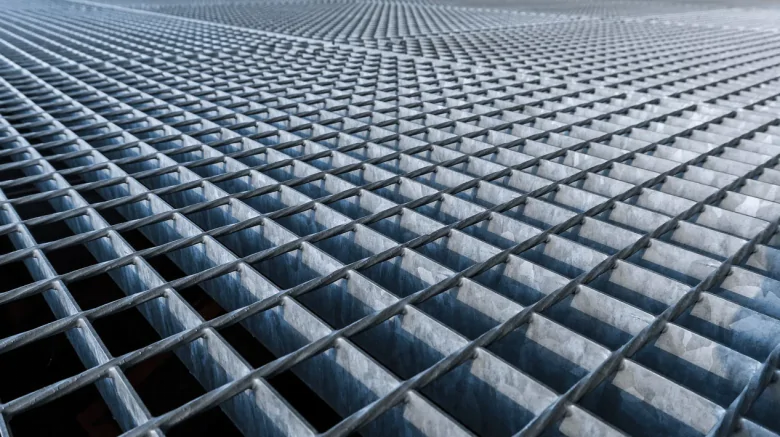
Steel grating is an indispensable tool in various industrial and commercial settings. In its most common applications, it helps keep workers and visitors in a facility safe, providing a stable flooring base and traction when walking at ground level and, especially, at heights.
With its large surface area and superior strength-to-weight ratio (and therefore low fatigue), steel grating is ideal for use in areas where heavy equipment is used or where public access occurs. Such as warehouses, industrial facilities, distribution centers, arenas, and convention centers – as well as any other setting in which safety is paramount.
As a material, they provide stable flooring that is typically level; they provide traction when walking at ground level. Most importantly, they give people working at heights a safe surface on which to stand. All of this is possible because of the interlocking features of the grid, which has long been a staple product in the railings market.
Manufactured from various materials, metal gratings have become an essential part of the design and construction of walkways, floors, and platforms for years.
2. The benefits suitable for underground applications
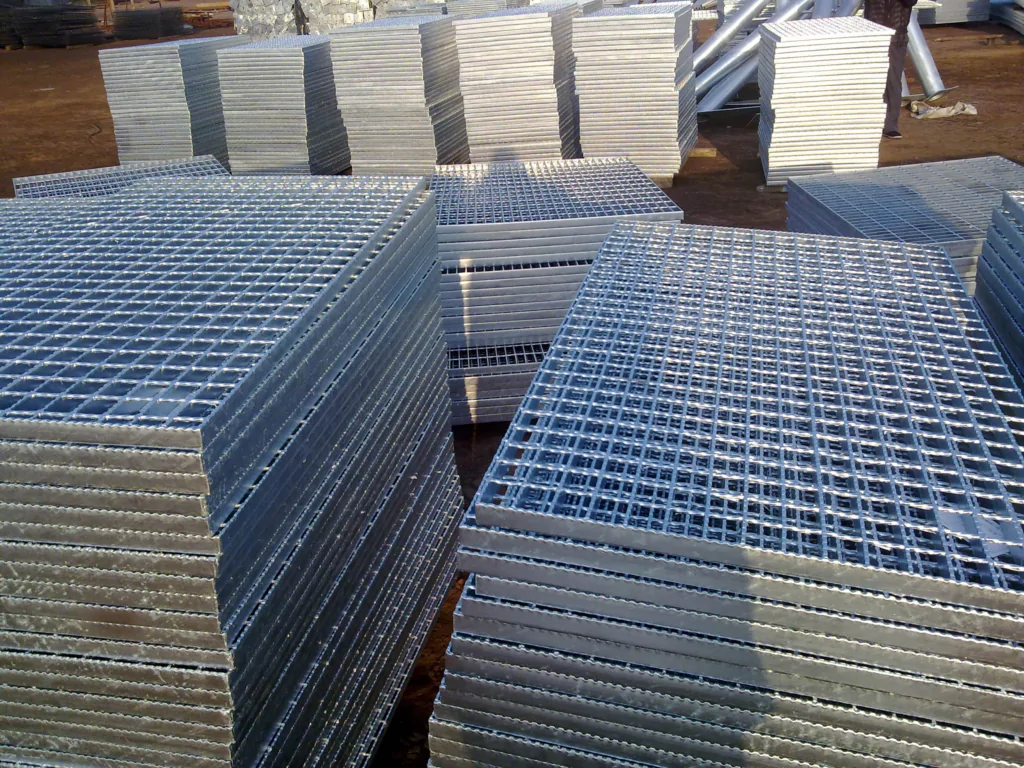
Tunnels require reliable support for their excavation, and steel gratings are the ideal solution. Their efficient design makes them more economical than traditional arching techniques while offering effective temporary primary support when conditions demand it.
From easily adjustable sections to cost-efficient uses of shotcrete – making a reasonable choice in grating can drastically reduce project costs and bolster progress like never before!
Great load capacity | Steel gratings can support much weight without collapsing, which is important in underground applications where the weight of the soil and any equipment or vehicles present can add up quickly. |
Durable | They will last longer and will not need to be replaced as often, saving costs in the long run. They are also less likely to be damaged by fire, chemicals, or other hazards that might be present in an underground environment. |
Safe | Seldom do they have sharp edges. This means that there is less risk of injury if someone were to fall on gratings or if they were to come into contact with gratings while working in an underground environment. |
Aesthetically pleasing | This means steel gratings can improve the look of an underground environment and make it more inviting for people to work. |
3. The underground applications of steel gratings
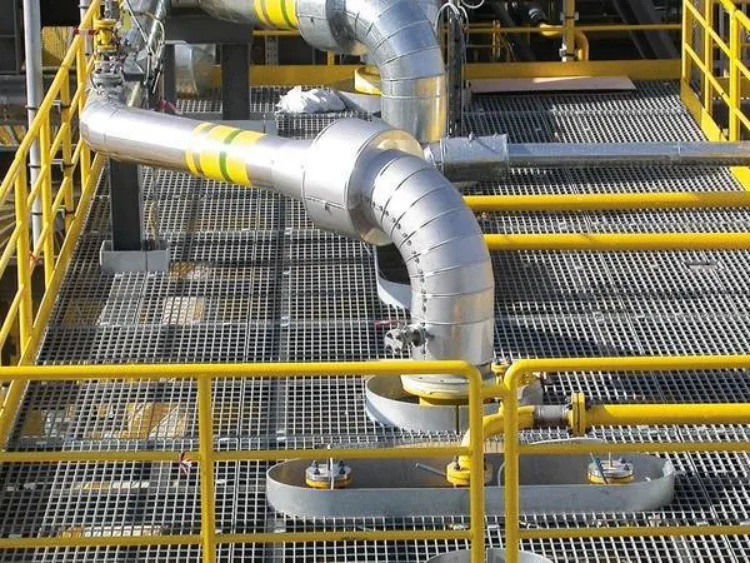
Steel gratings are commonly used for many underground applications. They provide a safe and reliable footing, especially in wet and slippery conditions.
- In sewers and underground pipelines, steel gratings are used as stair treads to facilitate the work of operators.
- They also have a variety of applications in the city’s drainage systems, such as covers above the trenches or other parts of drain water ditches.
- Bearing and cross bars make these gratings ideal for ventilation devices, allowing fresh air to enter underground spaces or warehouses.
- They can also be employed as rampways in underground parking lots since they can support cars without giving way during driving.
For particularly heavy-duty applications, galvanized welded or press-locked steel grating are recommended due to its strength and sturdiness.
In addition, steel gratings have also been installed in mines to ensure safety on slippery surfaces. They can also be placed around oil tanks to keep personnel from danger zones.
Lastly, they are an indispensable part of oil pits walls used for oil drilling operations. With the help of its high corrosion-resistance and durability features, steel gratings ensure that important industrial sites remain safe for workers at all times.
Grating panels are another option that is available for underground applications. These panels often include pre-punched bearing bars and heavy-duty load tables manufactured from hot dip galvanized steel or welded together using structural steel.
4. The common material used for underground applications
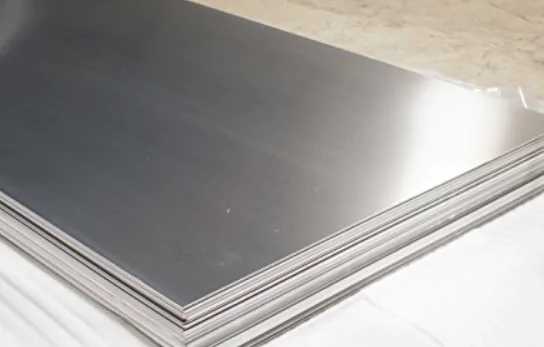
Carbon Steel
It is strong, durable, and relatively inexpensive compared to other options. The main advantage of carbon steel is its resistance to corrosion and ability to withstand extreme temperatures. It also has excellent ductility characteristics that allow it to be welded into complex shape configurations.
Stainless Steel
This material is also widely used in underground applications because of its superior corrosion resistance compared to carbon steel. Stainless steel has a much higher melting point than carbon steel and can withstand more wear and tear over time.
Aluminum
While aluminum isn’t quite as strong or durable as either carbon or stainless steel, it does have the benefit of being lightweight and relatively inexpensive. This makes it ideal for use in areas where weight needs to be minimized, but strength and durability are still important factors, such as when creating steel gratings for underground applications.
Additionally, aluminum won’t rust or corrode as other materials may, so it works well for long-term installations, even with wet conditions.

Fiberglass
Fiberglass doesn’t rust easily and is light enough that large panels can be placed without additional support structures. Additionally, fiberglass gratings are non-conductive, so they can provide extra insulation against electrical shock hazards if needed.
Heavy-Duty Grating
Heavy-duty grating is made from heavier gauge metal than light-duty gratings. So they are generally used when increased load capacity and strength are needed in an area prone to foot traffic or heavy machinery passing over them regularly due to their robust construction capabilities under these conditions.
Light-Duty Grating
Light-duty gratings are made from thinner gauge metal than their heavier-grade counterparts, so they are typically used in cases where a lighter-weight application is desired. But they still require some strength or durability under certain conditions, such as foot traffic passing over them regularly due to their lower profile construction.
While still providing ample support within confined spaces such as sewers or drains where clearance requirements must be met with limited space available.
5. How long will a steel grating last for underground applications

A steel grating can last a long time if appropriately used in underground applications, but the longevity ultimately depends on the type of material and finish used. Generally speaking, untreated steel gratings have a significantly shorter service life than those treated with either cold galvanized or hot-dipped finishes when placed in underground environments.
Cold galvanized steel gratings | Typically last between one and two years in a confidential setting |
Hot-dipped galvanized steel gratings | Can last up to 20-30 years |
Stainless steel gratings | For even more extended periods, often last between 20 and 40 years |
However, environmental conditions can affect the ultimate duration of usage for any grating. For example, extreme temperatures or humid conditions may decrease the longevity of any type of grating over time. It is important to consider such variables when selecting a grating for underground use.
Conclusion
Steel gratings are a versatile and durable solution for a wide range of underground applications. From drainage and ventilation to electrical and cable management, steel gratings provide a safe and functional option for underground environments.
Whether you are working on a construction project or looking for ways to improve the functionality of your underground space, steel gratings are a reliable and cost-effective option to consider.