Introduction
Welded grating is created to fulfill various purposes, from providing safety barriers to cranes, hoists, and machinery against heavy and shock loads in workshops, space structures, and industrial equipment.
As the demand for grating products is increasing, we take a look at the process of how welded steel grating is made.
What is a Welded Steel Bar Grating?
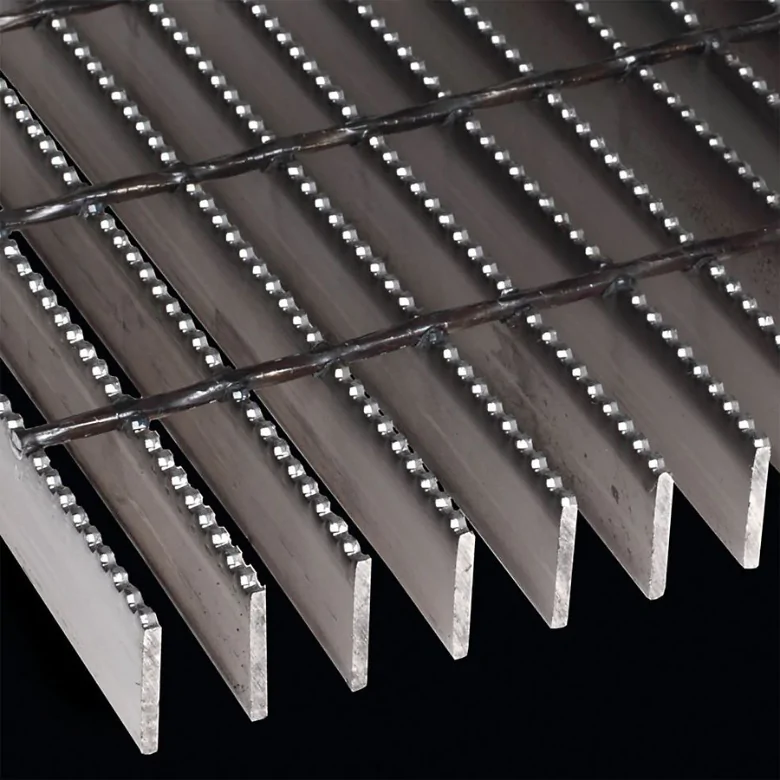
Welded steel grating is an economical design ideal for most industrial applications. It is manufactured by forge welding rectangular bearing bars and drawn cross bars creating a positive fused connection and providing years of service under the most demanding conditions.
Welded steel grating is designed to provide a rigid open-grid pattern that offers complete access to the entire smooth surface area of your products. The open practice allows maximum airflow and moisture removal while providing structural support and strength.
What are the Advantages of Welded steel grating
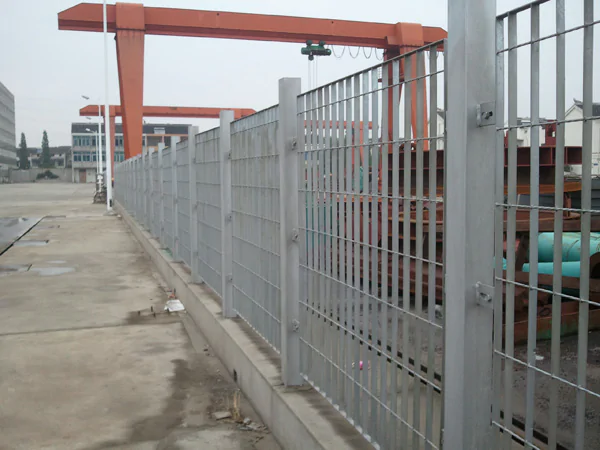
- Hot-dipped galvanized steel grating
The features have an attractive appearance, acid and alkali resistance, corrosion resistance, and rust resistance, and it has a long service life span, suitable for outdoor applications. It is the most durable one compared with other methods. Generally, it could last for more than 50 years.
- Cold-dipped galvanized/Electro galvanized steel grating
It is suitable for the dry environment, such as indoor applications. If used outdoors, in cold or damp environments, it only lasts for about 3 or 4 months for getting rust.
- Painted steel grating
Corrosion resistance at a medium level, moderate price, optional color. It costs less than the galvanized one. When steel gratings are used for machine equipment, they are often painted in the same color as the equipment, like grey or black.
- Untreated steel grating
Cheap, and suitable for indoor and dry environments, but quickly gets rusted in a wet and rainy environment.
Steps to make a welded steel grating
Step 1: Choosing the Material
When making a welded steel grating, selecting the suitable material is essential to ensure a strong and durable product. Carbon steel and stainless steel are the two most commonly used materials for this type of grating. Carbon steel is usually chosen if the application requires an economical solution with good strength, while stainless steel is typically used for more demanding applications that require higher corrosion resistance.
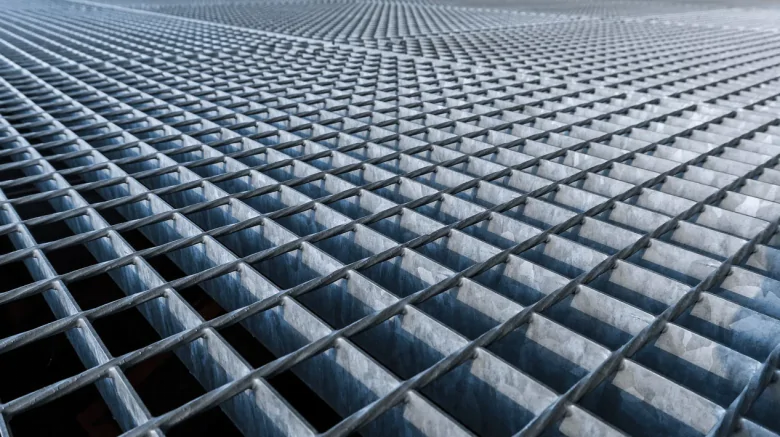
Step 2: Pressing/Welding
Once the ideal material has been selected, it needs to be pressed or welded into the desired shape according to the specifications provided by the customers.
In pressing, the metal sheets are pressed into a specific shape using a die, while in welding, two or more pieces of metal are joined together by heat and pressure from an electric arc or other welding processes. Both of these processes can produce quality gratings suitable for various applications.
Step 3: Cutting
After pressing or welding, the gratings will need to be cut into proper sizes per customer requirements. This step can involve manual cutting with saws or advanced CNC cutting machines, which are programmed specifically for the required shapes and dimensions. All cuts must be accurate and precise to ensure correct installation later on.
Step 4: Banding
Banding refers to wrapping strips of metal around each side of the grating to give extra support and protection against corrosion and structural damage caused by environmental factors such as moisture and temperature changes throughout its lifespan.
This is a crucial step that must be noticed; incorrect banding can lead to premature failure even when other measures have been taken correctly during the manufacturing process.

Step 5: Surface Treatment
Depending on client requirements, additional steps may be necessary before shipping out finished gratings, such as surface treatments like painting or galvanizing to provide further protection from corrosion or rusting over time due to exposure to different elements like UV radiation or salt spray from oceanic climates, etc.
This step also ensures that any sharp edges present after cutting have been smoothed down, which further improves safety standards during installation as well as the long-term performance of the product itself.
Step 6: Inspection
Before shipping out any finished product, all products must undergo a rigorous inspection to ensure they meet industry standards regarding quality and safety. This inspection should include visual checks along with physical tests like pull-out tests, which measure load capacity at different points across each grating panel, which all need to conform within acceptable limits before shipment can take place safely without compromising on quality aspects whatsoever!
Step 7: Packaging
Finally, muster with flying colors once the inspection has been completed successfully and all items have passed. They must then be carefully packaged according to customer requirements to arrive safely at their destination without being damaged during transit.
Since many steel gratings tend to be large items, special care must be taken when preparing them for shipment, especially if using standard shipping methods instead of custom-dedicated vehicles for delivery, etc. By following these steps closely, one can ensure that each batch produces high-quality welded steel grating that meets their exact requirements every time!
Tips for making a welded steel grating
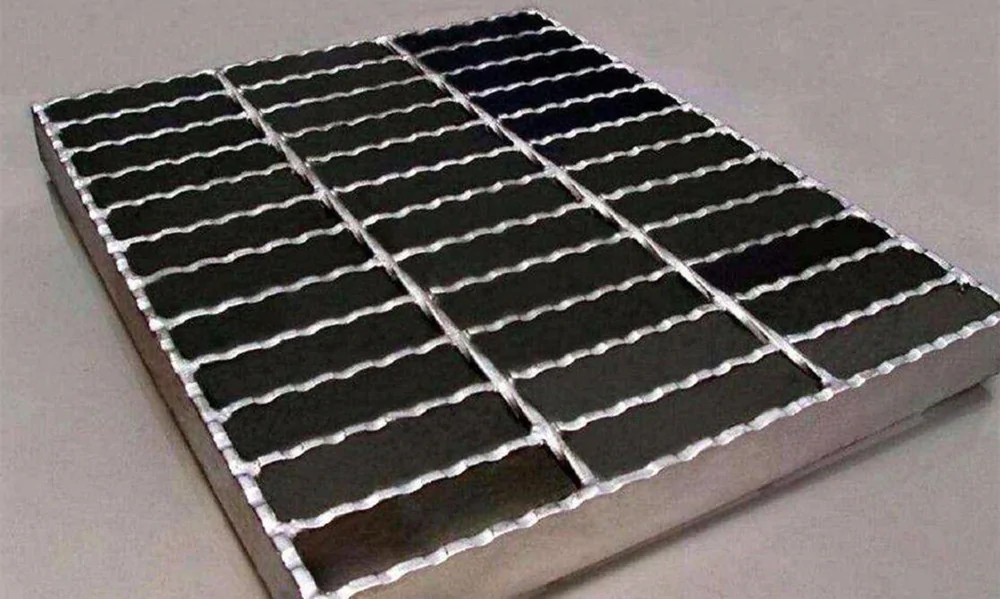
Choose the correct type of grating
First, make sure you know what type of grate you want. There are three types: safety grating, load-bearing bars, and welded steel gratings. Safety grating is often used for industrial applications because it has a serrated bearing bar that helps prevent slips or falls. It also has cross bar for greater strength and stability.
Load bearing bars are used when the load is distributed evenly across the surface area of the grate. Welded metal grating is typically used where storage containers are being unloaded onto trucks or trains because they’re resistant to corrosion and can be easily cleaned after use.
Choose a suitable material
Carbon steel, stainless steel, and aluminum are the most common materials used for steel gratings. Carbon steel is the most economical choice, but carbon steel is also susceptible to corrosion. Stainless steel is more expensive but is more resistant to corrosion. Aluminum is the most expensive but is also the most resistant to corrosion and has the best strength-to-weight ratio.
Choose the right finish
There are several finishes available for steel gratings, including hot-dip galvanized, painted, powder coated, and anodized. Hot-dip galvanized is the most economical choice, but it is less durable than other finishes.
Painted gratings are more durable than hot-dip galvanized gratings but are less resistant to corrosion. Powder-coated gratings are more expensive but have better resistance to corrosion and abrasion. Anodized gratings are the most expensive but have the best resistance to corrosion and abrasion.
Another popular option is metal open bar grating, with crossbars running between its support legs. These crossbars give the grate more rigidity and make it stronger than standard “box” gratings without sacrificing the ability to let light through them (such as those used on sidewalks).
How to use a welded steel grating

There are two kinds of processing steel gratings: Hand-welded and machine-press-welded
- Hand-welded steel grating
This can be used in various applications, such as drainage covers, platforms, stair treads, and pedestrian walkways. The manufacturing process is similar to the one for machine-press-welded grating but with more emphasis on welding.
First, holes are punched into the bearing bars and placed upright; then, crossbars are inserted into the punched holes and spot-welded together.
Although hand-welding may not provide as much strength as press-welding, it offers far more flexibility in terms of design. For example, it is possible to form complex shapes due to increased reach from manual welding.
Additionally, hand-welding also allows for customization in bar size and spacing. As a result, hand-welded steel grating offers an ideal solution for projects that require higher levels of aesthetic value or custom layout requirements.
- Machine-press-welded
Using a machine press-welded steel grating is reasonably straightforward. First, the bearing bars should be aligned in the desired configuration and attached securely to the frame. Then, the crossbars should be consistently placed on top of the bearing bars.
Finally, the welded steel grating is put under pressure using a hydraulic resistance welding automatic pressure welding machine. This ensures that all parts are joined together firmly and reliably through strong welding power and liquid pressure.
This technique provides steel gratings with superior durability, strength, and stability to traditional welding techniques. Using a hydraulic resistance welding machine also increases speed and efficiency when mass-producing steel gratings, making it a cost-effective solution for industrial applications.
Three packing methods for steel gratings
1. Packing goods in bundles, usually for relatively neat and flat steel gratings
2. Screw rod fixation, with four screws going through the aperture of the gratings and then locked with screws to ensure that all of the steels gratings are bounded together
3. Pallet packaging, generally used for export packaging, has two materials: Wooden and steel. Specific pallet packaging depends on the actual shape of steel gratings
Conclusion
These tips and tricks can help anybody have a better experience with welding. Start by learning from professionals so that you can start welding yourself. Next, try to make sure that you practice as much as possible. You might not feel like practicing when you first start, but all those hours working on your skills will pay off in the long run.