Introduction
Are you looking for the right surface treatment methods to fit your need? Do you know how to choose from different surface treatments according to your application? In this article, we’ll help you to determine which is the perfect fit for you.
In choosing the right surface treatment methods, architects and engineers needed new and improved finishes to guarantee the grating’s durability in particular settings and project conditions due to the various applications.
You can choose from having it mill-finished, black paint-finished, powder coating, hot dip galvanizing, and many more.
Would you like to know more about the different surface treatments so you can choose the one that will work best for your application? Continue reading.
What is Surface Treatment for Steel Grating and its Benefit
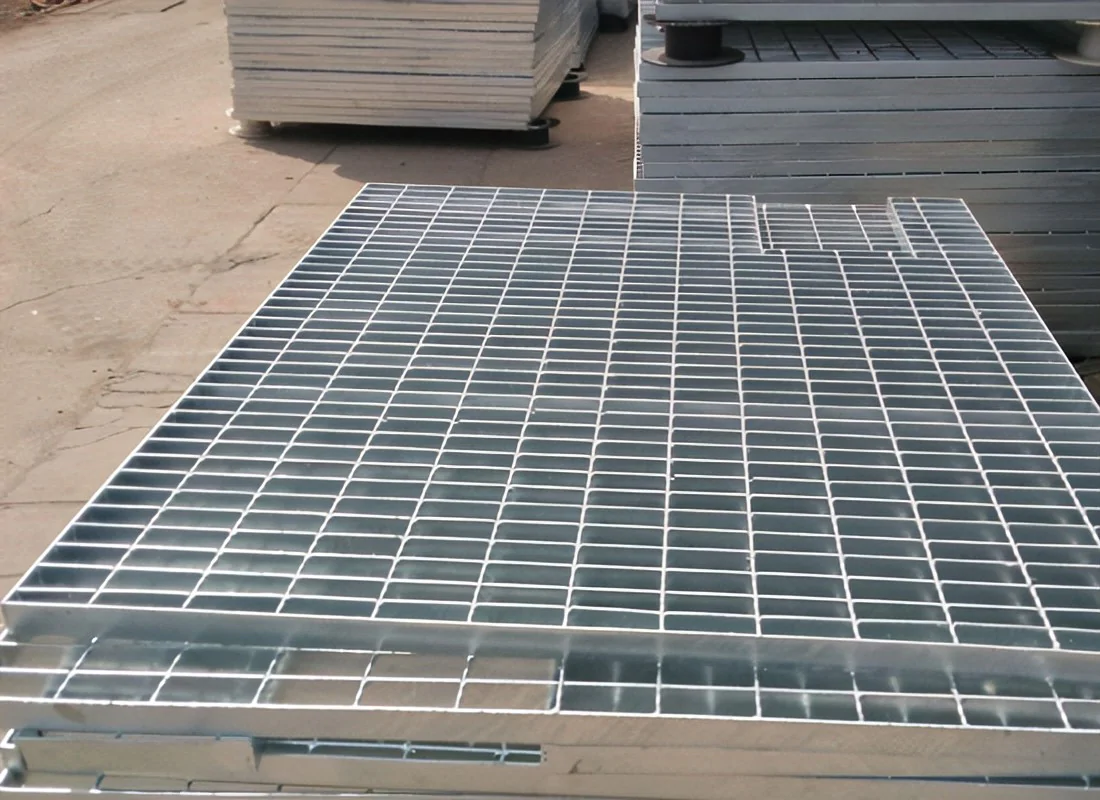
Surface treatment for steel grating is a process where the steel grating gets the finishes to have its lifespan be more productive and durable throughout its entire journey of the service environment.
Due to its modern appearance, architects are increasingly using it as an option for fences, facades, louvers, and other aesthetic components that complete residential or urban projects.
Here are the benefits of the steel grating has its surface treated properly:
- The best surface treatment methods can have the best materials to have long-lasting economical corrosion protection for your steel gratings.
- Make sure your surface will not peel off or crack under normal mechanical stress for example during transport or when walking or even driving on it.
- It will increase the lifespan even in highly loaded areas by using excellent products.
- It will prevent counteract contamination from machines and have an abrasion resistance feature.
The Different Types of Surface Treatment of Steel Gratings
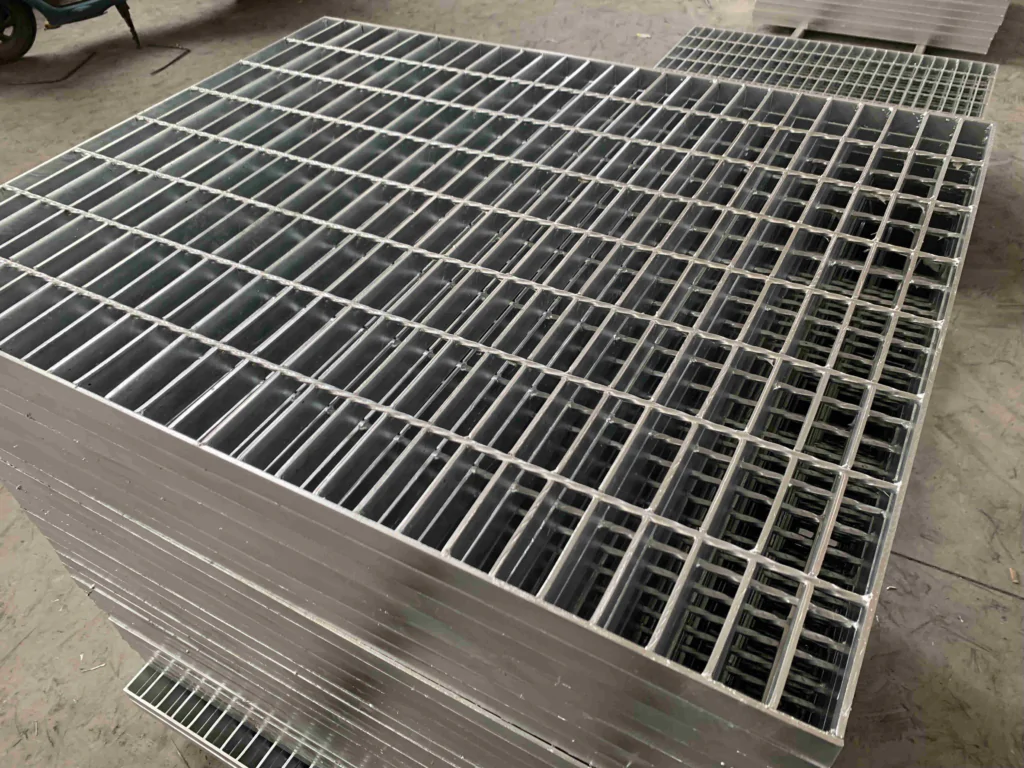
Here are the different types of surface finish for your steel gratings:
Mill Finish
The panel or specially-made grating is delivered unprotected and in its natural finish. This coating is utilized when a project calls for a natural steel color appearance, keeping in mind that its surface will corrode in a matter of days.
Black Paint Finish
It involves coating the grating with a thick layer of special black paint after submerging it in a black paint kettle. Steel can have long-term corrosion resistance because of this coating. Although not the most protective, this finish nonetheless prevents short-term corrosion of the object.
Powder Coating
This coating procedure involves spraying atomized paint particles onto steel to produce a more effective paint. Any other finish on the market is inferior to this one. As a result of the large range of colors it provides, architects choose to use it to coordinate colors in their construction projects.
It is advised to hot dip galvanize the item before powder coating it since this finishing procedure ensures an additional 5 to 10 years of working life.
Hot Dip Galvanizing
It is a method for protecting steel structural integrity to improve corrosion resistance by applying layers of zinc to them. The highest level of corrosion protection for any steel product is provided by this method, which is employed as a coating in industrial, civil, commercial, and municipal operations.
The galvanizing process involves submerging objects in a molten metal bath made primarily of zinc. The surface of the pieces is entirely covered and shielded from the corrosive impacts of the service environment since they are completely submerged in liquid metal.
The finest corrosion protection currently on the market is this. The finishing procedure is carried out following ASTM-A-123 guidelines. Its durability in harsh circumstances makes it suitable for all projects.
Given that the majority of the covering is made of zinc, it not only increases the product’s lifespan by up to 60 years but also has a contemporary grey finish that exudes elegance.
Galvanized and bituminized
Because bitumen (Inertol) offers high resistance to such media, bitumen dipping is frequently used in acidic environments. The galvanizing serves as a superb primer for the bitumen coating, extending the life of our products even in heavily trafficked areas just like in other methods.
Galvanizing services are offered for a variety of industrial goods. Among many more, examples include industrial grating, pipes and tubing, angles, beams, channels, and railings.
Since it offers an alternative to the use of durable, cost-effective, and resistant buildings, this approach is economical and appealing to the construction sector.
Pickled
A passive layer that is unseen prevents corrosion in stainless steel. Pickling is a chemical surface treatment used to prevent contamination from mechanical properties and to provide an effective passive layer.
Anodized
An oxide layer of protection is created on aluminum via the anodizing process, a surface technology technique. Usually, anodizing is done on decorative sections of aluminum to give it a consistent appearance. Additionally, many color hues can be produced.
How each Type of Surface Treatment is Processed
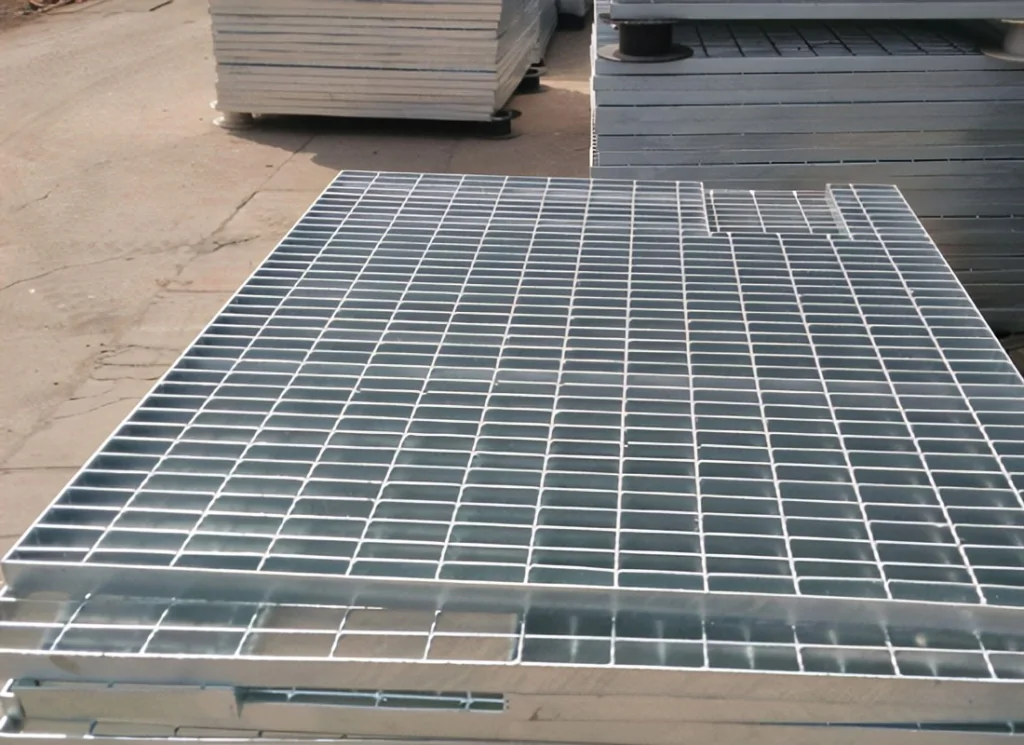
Here is the process of how each type of surface treatment is made:
Mill Finish
Stainless steel is “cold rolled” using specialized rolls or dies to get the finish. The surface is smoother and less pitted as a result of the cold rolling. It is then dissolved in acid to soften and descale it. For one last pass on polished rolls, the steel is given to further improve its smoothness and prevents to have sharp edges.
Black Paint Finish
The steel gratings are painted mostly in black oxide for the advantage of not being too reflective or so.
Powder Coating
A spray cannon is used to apply powder to metal during the electrostatic powder coating process, and then the powder-coated object is baked. The powder melts to create an even coating, and when it hardens, it hardens into a fashionable, protective, and durable covering as one of the important factors.
Hot Dip Galvanizing
When the grating is submerged in a bath of liquid zinc heated to about 450°C, an iron-zinc alloy coating forms, completely covering the grating in zinc.
Galvanized and bituminized
The galvanizing process will serve as a primer before dipping bitumen to protect the steel gratings from an acidic environment.
Pickled
A thin surface layer is removed from the stainless steel gratings during pickling using an acid solution, typically a hydrofluoric and nitric acid mixture to have its chemical exposure.
Anodized
A method of electrochemistry that results in an oxide coating that adds corrosion resistance and a decorative finish.
How to Choose the Right Surface Treatment for Your Needs
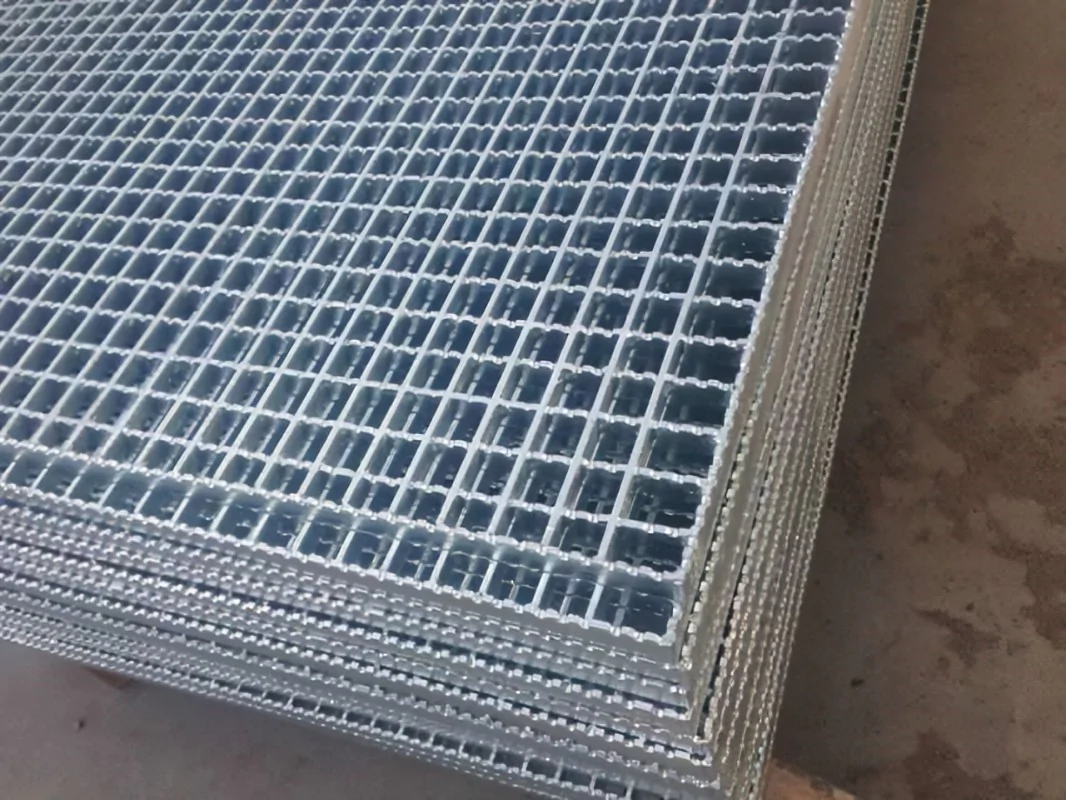
Here are some tips to follow in choosing the right coating treatment for the surface of your steel gratings according to your needs:
- Determine which of the friction, wear, and corrosion limiting key factors affects bearing life.
- Make a list of potential protective coatings and surface preparation, removing any that are deemed inappropriate due to thickness or other processing requirements.
- To confirm the suitability of the process and create a short list of preferred candidates, whenever it is practical to do so, consult prior case histories of comparable applications.
- To choose the best process for coating selection, refer to detailed surface engineering specifications.
In addition to these guidelines, it is advised that appropriate qualification trials be conducted before a particular process is selected to confirm its suitability, especially where there is little or no proven record of a process for the application.
Common problems of Surface Treatment

Here are the common problems that a surface treatment can do to your steel gratings:
Loss or Aggregate
- The binder was sprayed before the cover aggregate was laid, which gave the binder time to cool and set. The adherence of aggregate particles to the binder is impacted by a dust or moisture film or coating on the particles. Before full adhesion, fast traffic is authorized.
- A downpour happens before adhesion forms.
- If the aggregate is placed in excess, it could cause embedded aggregate to move beneath traffic.
Poor adhesion or Bond to Road Surface
Although it is uncommon and is therefore not included as one of the significant flaws, the full loss of surface treatment can happen. The following factors may contribute to a surface treatment’s failure to adhere well to an existing surface:
- a dusty coating or film
- following wet weather, moisture was found on the old surface
- low surrounding temperature
- using a binder that is excessively viscous while applying rock
- when the seal coat was applied, any combination of these was possible
Streaking and Flushing
One of the most frequent flaws in surface treatments is the application of an excessive amount of bituminous binder.
The black and frequently sticky surface condition known as flushing, bleeding, or fattening up, which can cause a reduction of skid resistance, is caused by excess binder exuding upward onto the pavement surface.
Using abrasion incorrectly
This error, which is more frequently made by manufacturers when applying composites and metals, is typically caused by either over or under-abrading a surface. However, utilizing abrasion at all could be a mistake for producers with polymer-related applications.
Make sure the base material you are abrading needs to be abraded to adhere. Additionally, be aware of the precise level of abrasion required and put in place a verification step to make sure it has been met and not exceeded.
Conclusion
With the help of this succinct explanation of various steel bar grating finishes, you can now advise your project manager on the best course of action to guarantee the project you’re working on will be aesthetically pleasing and durable in choosing the right coating for your steel grating.
If you still have questions, don’t be afraid to ask a professional.