Introduction
Are you curious about how to make steel gratings? Do you know that there are steps in its manufacturing process of it? Look no more because here’s an article that will guide you through it step-by-step! Take notes with this information.
To produce a high-performance grating, the process of making it uses the most cutting-edge production equipment, serial manufacturing that is sorted, and intelligent planning and control software. Structure and manufacturing methods that adhere to lean management concepts.
This translates for the client into effective planning, quick turnaround times in bar grating production, and strict adherence to delivery deadlines. Continue reading to know more about its process.
1. Choosing Material
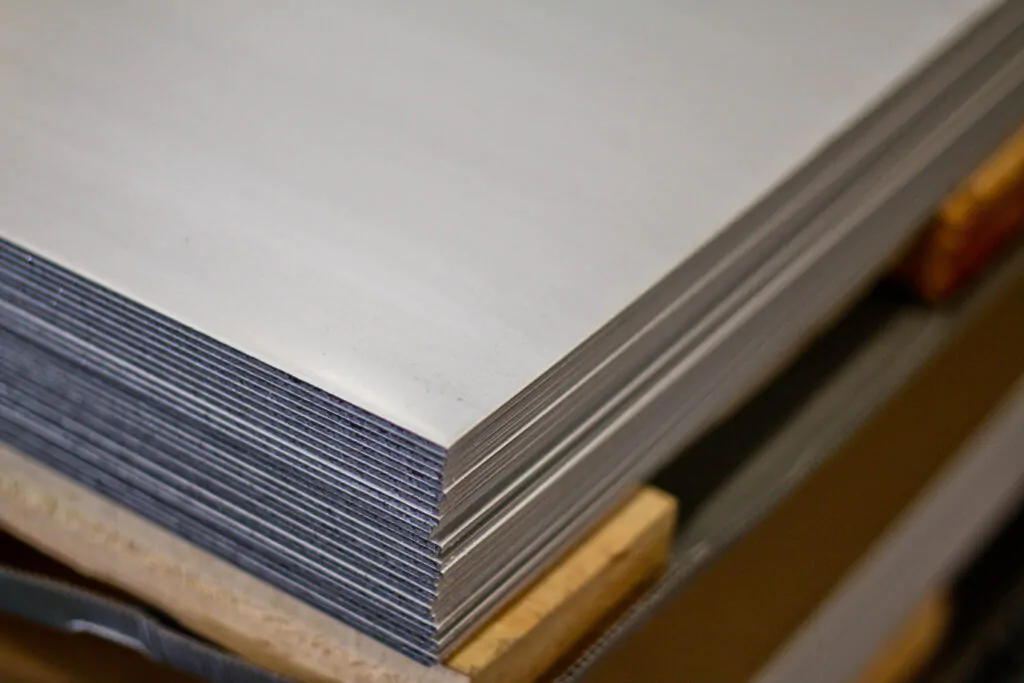
Steel gratings’ raw materials are coils of steel in a range of strengths and widths. The quickest delivery times are ensured by a large raw material warehouse of split bands or slit coils. Carbon steel, galvanized steel, or stainless steel are all acceptable raw materials for steel bar gratings.
Low-carbon mild steel is the most popular option since it is affordable and simple to weld.
Bar grating comes in a wide variety of designs, materials, and uses. Determining the best fit for design and functional requirements can occasionally be difficult due to the abundance of possibilities.
All the materials must be cut to size and thoroughly cleaned to get rid of any dirt, grease, or other contaminants to maintain this process flow. Not to mention, before being approved, the raw material must pass quality control.
Know the applications
When high levels of strength and durability are required, bar grating is the best alternative. Because of its excellent performance and low maintenance requirements, it performs well in harsh and challenging situations.
To choose the best bar grating for your project, it is first useful to think through the precise application for the product. Knowing the application will assist you through the other stages of the hiring process.
Know the grating types
The major material, whether it be lightweight aluminum, robust carbon steel, or corrosion-resistant galvanized steel and stainless steel, depends on several aspects, including strength, weight, environment, and aesthetics.
Depending on your demand for traction, choose a surface that is smooth, serrated, or grooved. Verify that the application loads your chosen grating can manage. There are load tables that make it simple to determine and validate load capacity.
It is crucial to remember that these are only a few factors to take into account when specifying bar grating. The best product for your application depends on specifics like series type, product spacing, bar size and shape, percent open area, and span.
2. Pressing / Welding
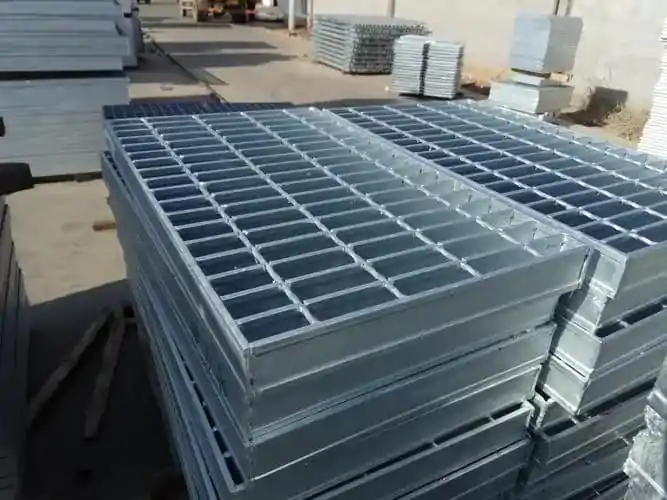
In a grating with a mesh hole structure known as a “pressed steel grating,” the cross bars are pressed under intense pressure into the bearing bars. This product is made of aluminum, stainless steel, and low-carbon steel.
Pressed steel grating is created by cold pressing the cross bars to the bearing bars under a load pressure of 500 tons.
For hand-welded steel gratings, workers first punch in the bearing bars, make them stand upright, and place the cross bars in the holes they drill. Then, by the way of spot welding, the cross bars and the bearing bars are integrated.
For machine-press-welded steel gratings, workers use the hydraulic resistance welding automatic pressure welding machine. The manipulator will automatically put the hollow tube cross bars on the bearing bars aligned evenly, and press the formal ones into the latter ones by welding power and liquid pressure.
To maintain the great stability of the grating, machines apply intense pressure to the deep rectangular cross bars as they are inserted into the grooves of the bearing bars. Robotic welding machines join the borders and the pressure-locked gratings.
The cross bars are welded to the sturdy bearing bars with pressure-welded gratings using resistance welding techniques.
Electro-forging and electric welding are both thermoelectric processes in which heat is produced by the movement of electric current where bent connecting bars extend the current flows through the junction region of the pieces that need to be welded for a predetermined amount of time and under a predetermined pressure.
Without the use of extra materials, metals are welded throughout this production process. This is accomplished by applying pressure and an electric current to the desired welding location.
To ensure a solid and consistent electrical connection, welding machine electrodes force metal components (often steel) together during the welding process.
The deeper cross bar serving electricity then flows through the electrodes, heating them until their connection site melts. The two molten metal pieces are combined and joined together. Both pieces solidify when the current is stopped, creating a strong metallic bond between them.
3. Cutting
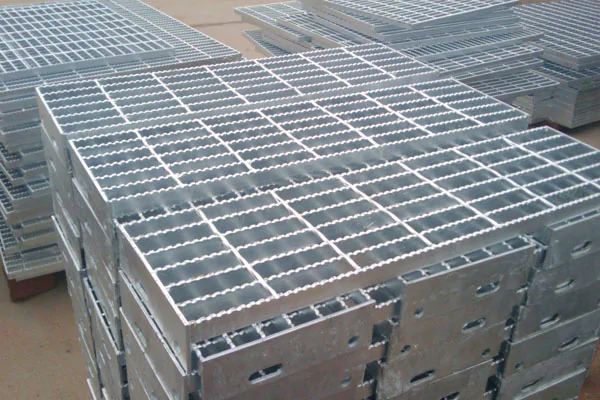
The major focus of steel grating edge preparation is trimming and rounding off the benefits of steel gratings. Any edges that are rough or sharp and could cut someone should be removed. This also gives the grating a more polished appearance.
Additionally, the edge preparation assists in avoiding rust on the grating for thick bearing bars.
It is necessary to cut the gratings created in this bearing bar spacing ranging into a cell that is the proper size. The grating structure is bonded and the bent connecting bars extend to the bearing bars and cross bars.
Be aware of the safety measures before cutting
- To prevent foreign items from splashing into the eyes and to lessen dust inhalation, the operator should put on safety goggles and a mask before beginning the grid plate-cutting procedure.
- To stop dust from irritating the skin and triggering allergies, wear gloves and overalls.
- Pick a site that is well-ventilated and well-lit for cutting thick bearing bars.
- Before cutting, make sure that all power instruments are secure and safe.
- This is a comprehensive list of steel grating cutting techniques; make sure to strictly follow them and put safety first.
Prepare the cutting tool
You can use a portable cutting machine tool, automated grating shear, band saws, cold saws, manually using gas torches, electric saws, or hacksaws. Traditional cold saw and band saw tooling requires routine sharpening or tool replacement, which results in downtime.
Shear tooling reduces unnecessary downtime during tool changes by lasting hundreds of times longer than standard tooling.
Choose the grating cutting style
Four-sided edging, three-bread, adjacent edging, opposite edging, smoothing, rounding, and square are typical cutting patterns and bearing bar spacing ranging for steel gratings.
Start cutting
We must first cut the grid plate before putting it on the grating board. The grid plate can be reasonably processed and cut to maximize economic value without compromising the grid plate’s inherent performance, depending on the size requirements and installation needs of the customer.
To ensure that the grid sheet’s corrosion resistance is not compromised after cutting, the cut surface of the deeper cross bar and cross bars running perpendicular must be coated with resin.
Cutting method
You can choose between straight-line cutting or curve cutting.
4. Banding
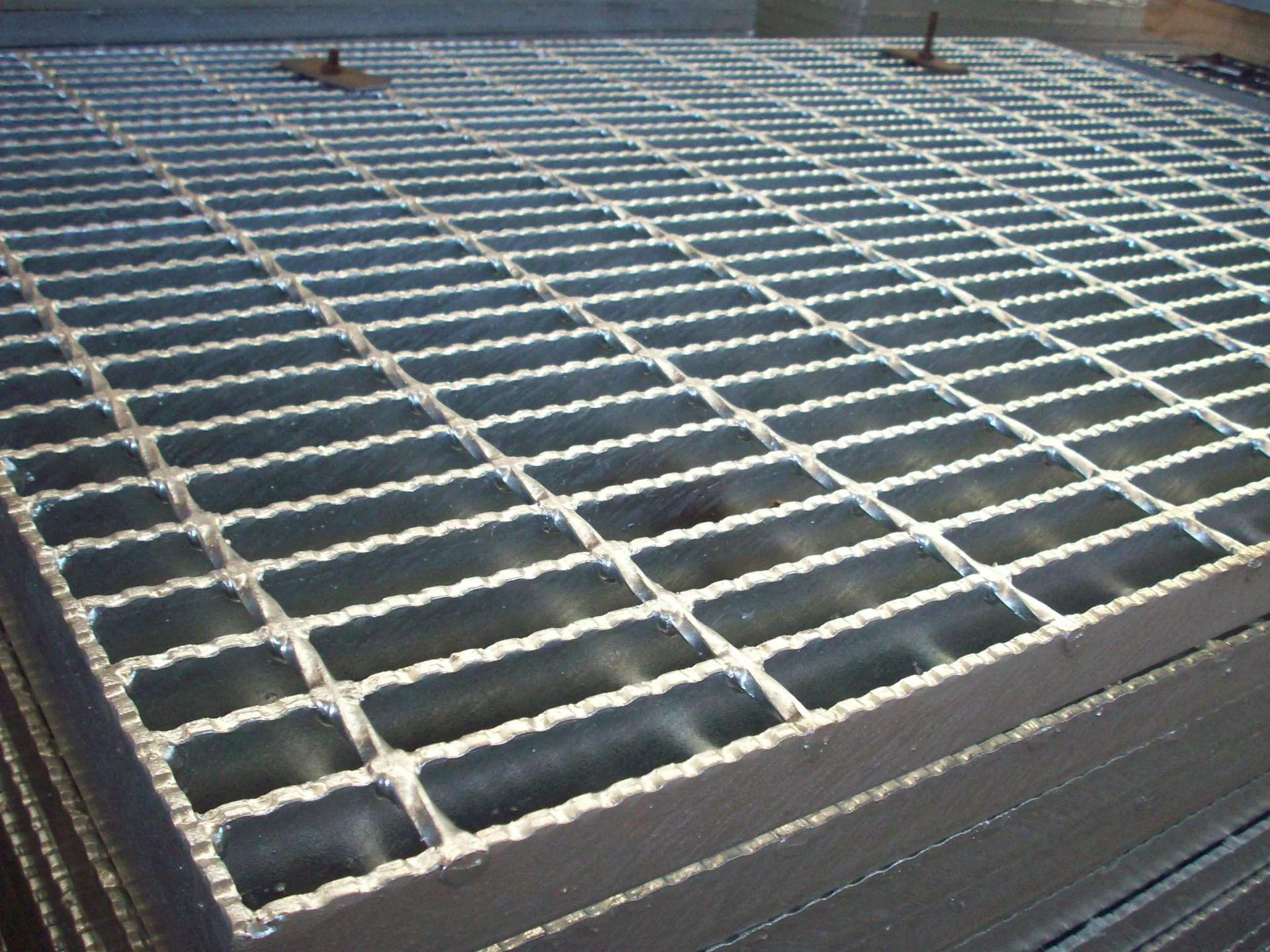
The grating panel’s open ends can be protected with banding. Any grating product may include a banding specification. Metal bars are welded to the open ends of the grating panel during the banding procedure. Banding, which adds additional transverse stiffness and a finished architectural appearance, significantly benefits some applications.
The following applications should always include a banding specification:
- Panels with removable grating that has a closed end increase worker safety during handling.
- Vehicle load exposure is when the band metal bars increase resistance to grating deformation brought on by recurring traffic patterns on open-ended grating by shifting loads to adjacent bearing bars and thereby reducing impact stresses of pre-punched bearing bars.
- Another choice is trench banding, which elevates the band bearing bars over the bottom of the bearing bars. Since it allows liquids to travel through and won’t cause liquids to become trapped between the band bearing bars and the metal grating support, the elevated band bar is perfect for drainage applications.
- Standard Trim and Optional Load Banded are two banding welding possibilities. Standard trim banding guarantees welds +/- 5″ on center and gives each item a consistent termination.
- In addition to providing a uniform end finish, load banding has welds at each bearing bar that help distribute the load across the metal grating panel.
5. Surface Treatment
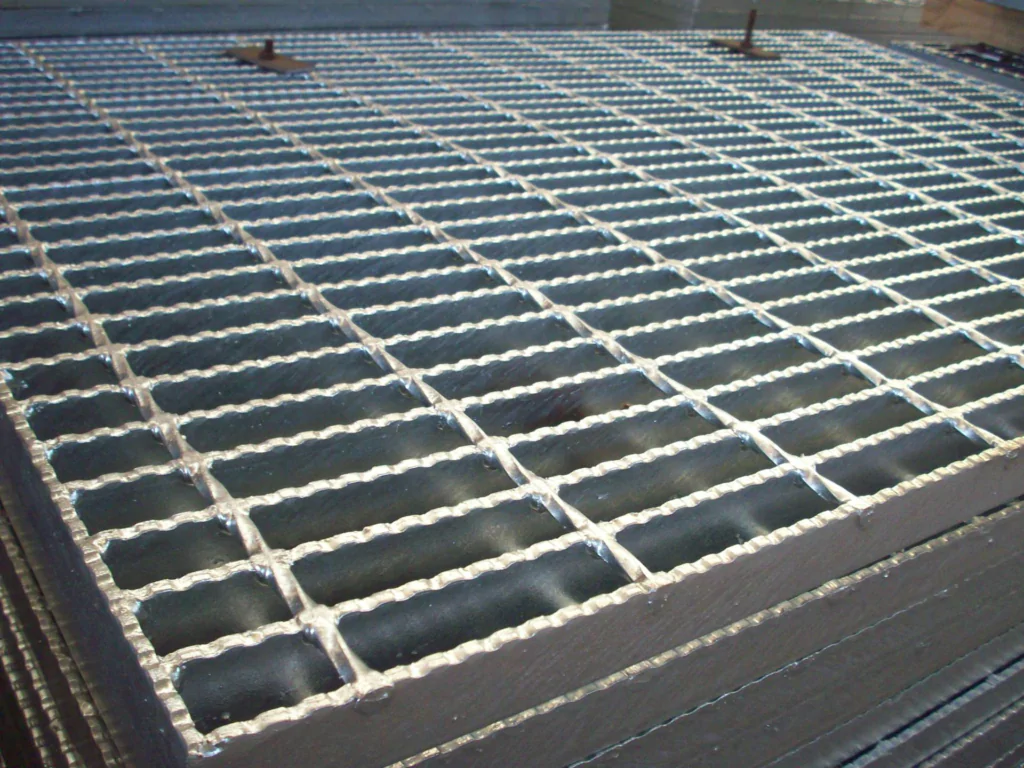
There are seven types of surface treatment for steel gratings:
Mill Finish
It’s the process where the stainless steel is “cold rolled” using specialized rolls or dies to get the finish. The surface is smoother and less pitted as a result of the cold rolling.
Black Paint Finish
This type of surface treatment is where steel gratings are painted mostly in black oxide.
Powder Coating
It’s the treatment when a spray cannon is used to apply powder to deep cross bars running perpendicular during the electrostatic powder coating process, and then the powder-coated object is baked.
Hot Dip Galvanizing
Hot dip galvanized is when the metal grating is submerged in a bath of liquid zinc heated to about 450°C, and an iron-zinc alloy coating forms, completely covering the metal grating in zinc.
Galvanized and bituminized
It is where the galvanizing process will serve as a primer before dipping bitumen to protect the steel gratings from an acidic environment just like in the process of hot dip galvanized.
Pickled
It is where a thin surface layer is removed from the stainless steel gratings during pickling using an acid solution, typically a hydrofluoric and nitric acid mixture to have its chemical exposure.
Anodized
It is the method where electrochemistry results in an oxide coating that adds corrosion resistance and a decorative finish of drawn cross bars.
6. Inspection

We established several steel grating inspections for quality control during manufacturing as part of the growth of the enterprise system. Additionally, we will recheck the items before delivery to make sure they are all in excellent shape and qualify for our consumers. The following are the inspection items:
Appearance assessment
To ensure a smooth and integrated surface and look, each steel grating will be examined individually. If there are any flaws, a qualified product will be chosen to take their place.
Size examination
Meter rulers, vernier calipers, micrometers, and other expert measurement tools will be used to inspect the width, length, and height of the product, regardless of the sheet thickness, bearing bars and cross bars sizes, or the total size.
All sizes must comply with both the requirements of the customer and the international standards’ tolerance.
Examination of performance
The load performance of the steel bar grating will be sampled and inspected following customer requirements and international standards. Additionally, the steel bar items will be provided with the test result.
Package examination
The most common packaging for steel bar grating is a steel belt, however, it can also be a wooden or metal pallet. Each package’s weight and quantity should be determined by the specific circumstances and demands of the clients. For the package to withstand the high impact during transportation, it must be rigid and firm throughout.
Label examination
Before delivery, the products will have labels attached. Brands, the company, specifications, quantity, and standards will all be listed on the label. Other information will be tailored to the needs of the customer.
Inspection for quality certification
The products will be provided with quality certification. Results of inspections, including those for appearance and performance, will be included in the certification. Additionally, raw material mill certification can be delivered concurrently following customer needs.
7. Package
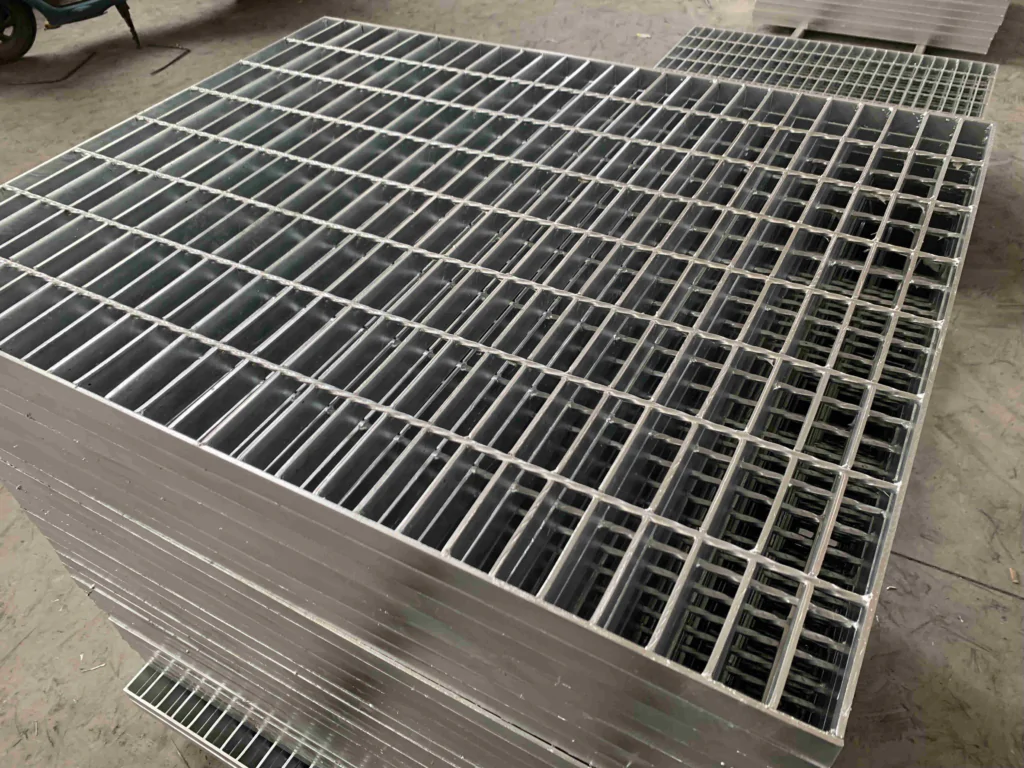
Custom-built bar gratings are delivered completely on schedule and to specifications. Standard industrial bar gratings are constantly on hand and ready to be delivered from our completed goods warehouse in a variety of standard diameters.
The use of top-notch packaging supplies is essential to preventing product damage during transportation. Steel bar gratings need to be packed with particular care and consideration.
Put the grates in a box or crate, wrap each one in a sheet of plastic film, and fill the spaces between them with packing material like bubble wrap or styrofoam.
Tape the box or crate shut, then write the date and contents on the outside. These packing suggestions will assist in preventing rust and corrosion on your steel grates while they are being transported or stored.
Conclusion
Steel bar grating is a type of metal product created by piercing metal sheets or connecting metal bars to create a grid. Engineers and designers collaborate to create metal grating solutions that perfectly match a structure’s specifications. Depending on the materials used and the method of production, a different process is used to create each shape and type of bar grating.