A sequence of metal sheet or carbon steel bearing bars that have been welded stainless steel grating together to form perpendicular bars make up steel grating. This produces a panel that can support a lot of weight. They are frequently utilized in paper mills, chemical plant walkways, and oil rigs.
For steel grating to handle the required weight loads, precise measurements of thickness are required. Continue reading to learn more about it if you are a business owner or contractor seeking high-quality steel.
What is steel grating
Steel grating, a prominent element in the field of architecture and engineering, is a framework of parallel or cross bars usually made from metal. Its robust and versatile nature lends it to various applications including industrial platforms, walkways, drain covers and stairs, offering both safety and durability.
The importance of selecting the right thickness
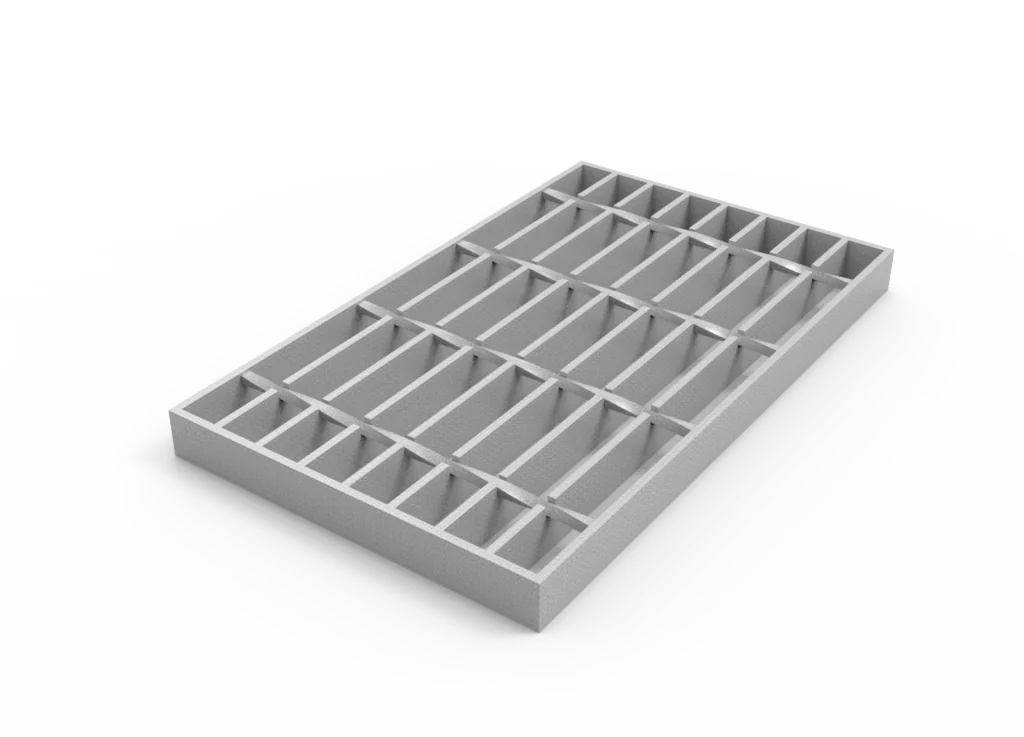
When venturing into a project that involves the use of steel grating, have you ever wondered about the significance of the thickness of the steel grating? Does it really matter? The answer is a resounding, yes.
The failure to consider the right thickness may lead to project delays, safety risks, and unnecessary costs. Let’s have a look at these factors.
A. Safety
The thickness of the steel grating significantly influences the safety of the structure. A thicker grating provides better strength and durability, essential for high-traffic areas. It reduces the risk of breakages or accidents due to structural failure. Thus, choosing the appropriate thickness for your steel grating is absolutely critical for maintaining safety standards in any environment.
B. Cost-effectiveness
Choosing the correct thickness for steel grating can be a cost-effective decision in the long run. While a thicker grating could be more expensive upfront, it generally lasts longer and can withstand greater weight and pressure, reducing the need for frequent replacements. In contrast, opting for a cheaper, thinner grating may lead to higher maintenance costs and a shorter lifespan.
C. Durability
Durability is another significant factor affected by the thickness of your steel grating. A thicker grating will be more resistant to wear and tear, allowing it to maintain its structural integrity for a longer time. This is especially important in harsh environments or heavy-duty applications where the grating is subjected to substantial stress.
D. Maintenance
Lastly, the thickness of steel grating also impacts the amount of maintenance required. Thicker grating is likely to need less frequent repair and replacement, saving you time and labor costs. It is essential to consider this while selecting the thickness of your steel grating to ensure it remains functional and safe for an extended period.
Knowing various steel grating thicknesses
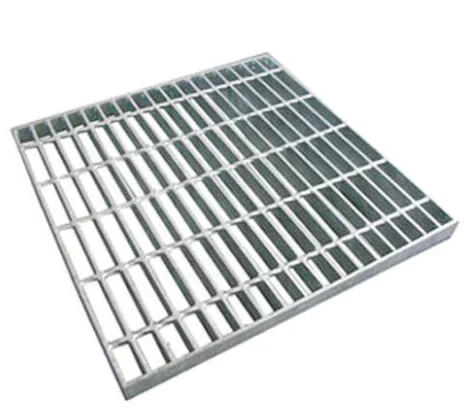
The thickness of steel grating is crucial as it directly impacts its strength and load-carrying capacity. This measurement generally relates to the thickness of the load-bearing bars, which are the primary structural element of the grating.
Common thicknesses typically include 1/8 inch to 1/2 inch, but other thicknesses might be available as well. Thicker bars are usually selected for heavy-duty applications where high load-bearing capacities are required.
The right thickness selection ensures the steel grating can handle the weight it’s designed for, contributing to the safety and reliability of the system where it’s installed.
Factors to consider when choosing steel grating thickness
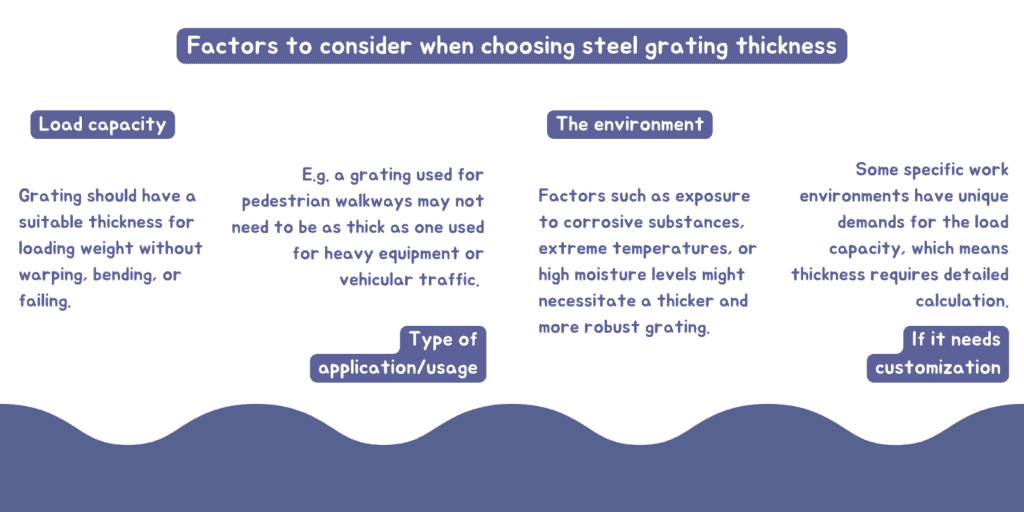
Choosing the appropriate thickness of your steel grating is a critical decision that can impact its performance, durability, and safety. Here are some key factors to consider:
A. Load capacity
This is the first and most crucial factor to consider. The steel grating should have sufficient thickness to carry the expected weight without warping, bending, or failing. The greater the weight load, the thicker the grating you’ll need to ensure safety and performance.
B. Type of application/usage
The way in which the grating will be used significantly influences the thickness selection. For example, a grating used for pedestrian walkways may not need to be as thick as one used for heavy equipment or vehicular traffic. Likewise, a grating used in a storage facility might need to be thicker, depending on the weight of the stored items.
C. The environment where it will be installed
The environmental conditions in the area where the steel grating will be installed also play a critical role in thickness selection. Factors such as exposure to corrosive substances, extreme temperatures, or high moisture levels might necessitate a thicker and more robust grating. Also, if the grating is to be installed in a high-traffic area, it would need to be thicker to withstand the constant wear and tear.
D. If it needs customization
When it comes to specific work environments that have unique demands for the load capacity of stainless steel gratings, such as a port or a wharf, large construction sites, chemical engineering fields, and offshore oil drilling platforms, it is typically the design organization or the user organization to customize the thickness and other specifications.
E. Unit of measurement
For purposes of general standards, we frequently use one inch as the unit of measurement for steel grating thickness. Additionally, a number that is surrounded by double quotes, such as 1″, denotes one inch. Regularly a sixteenth of an inch or a quarter of an inch, also participates in showing the thickness. For instance, 1-3/16″ denotes one and three-sixteenths of an inch, and 1-1/4″ denotes one inch and a quarter.
How to choose the thickness for different applications
1/8 to 1/4 inches | 🏭Factories, warehouses, construction |
1/4 to 3/8 inches | 🏗️Decks, walkways, shopping malls, office buildings |
3/8 to 1/2 inches | 🚉Airports, train stations, bridges |
When selecting the appropriate steel grating thickness for varying demands, it’s important to factor in the specifics of your project and the prospective environment. Here we highlight the ideal steel grating thickness for several common applications.
A. Industrial Use – Factories, Warehouses
Typically, these spaces require a durable and robust material able to endure the constant stresses of heavy machinery and frequent foot traffic. In these cases, a thicker steel grating would be advantageous. A thickness of around 1/4 to 3/8 inches would usually be suitable, but the exact necessity may vary based on individual requirements.
B. Construction Sites
Construction sites are renowned for their harsh conditions. Therefore, a sturdy and high-load bearing steel grating is essential. However, the thickness required can often be reliant on the specific type of construction work being done. Generally, a thickness of 1/4 to 3/8 inches should suffice.
C. Residential Use – Decks, Walkways
In domestic scenarios, aesthetic appeal is often equally as important as durability. Thinner steel grating is more visually pleasing and less intrusive, but it must also be strong enough to accommodate regular foot traffic. A thickness of around 1/8 to 1/4 inches would usually be ideal for residential use.
D. Commercial Use – Shopping Malls, Office Buildings
Commercial environments necessitate a balance of durability, aesthetics, and pedestrian safety. For such applications, the thickness of the steel grating should be selected with these factors in mind. Typically, a thickness of 1/8 to 1/4 inches works well.
E. Transportation – Airports, Train Stations, Bridges
In areas with considerable foot and vehicular traffic, durability and safety are key. The steel grating thickness should be capable of withstanding the high-traffic and weight demands, suggesting a thickness of 3/8 to 1/2 inches. Remember, these are just guidelines, and the exact thickness required may vary depending on the specific demands of your project.
Common mistakes to avoid when choosing thickness
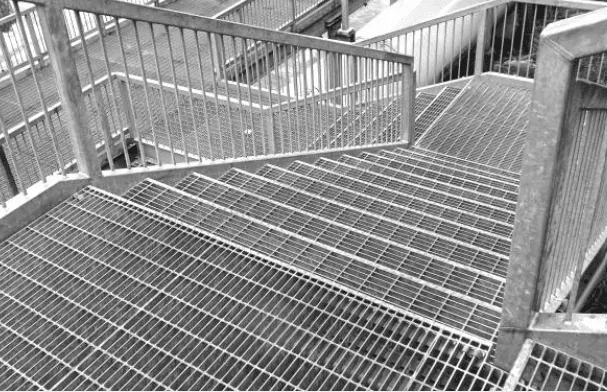
A. Overestimating weight load capacity
Remember, higher thickness does not always equate to higher weight load capacity. It’s essential to consult the manufacturer’s data and understand the weight that the grating can safely bear. Overloading can cause the grating to warp, crack, or in worst cases, lead to catastrophic failure.
B. Ignoring environmental factors
The grating’s thickness may need to be adjusted based on factors such as temperature swings, the presence of corrosive materials, or high-humidity conditions. Thicker grating might be required in harsher environments to withstand degradation and ensure longevity.
Conclusion
Remember that steel grating is an investment in safety and sustained productivity. Take your time, weigh your options, and make an informed decision. Your choice should be guided by careful consideration of your specific needs and the demands of your application.
Thank you for reading this guide. We trust that you now have a deeper understanding of the importance of choosing the correct steel grating thickness, and that you will utilize this knowledge in your future projects.