Introduction
Are you looking for an efficient and durable solution to cover your bar grating needs? Carbon steel gratings could be just the answer. These solid and lightweight materials are highly versatile, making them suitable for various applications.
In addition, carbon metal grating offers several advantages over other material types when it comes to creating custom projects – from engineering structures to construction projects or even home improvements.
So if you’re looking for a cost-effective way to add value and strength without sacrificing safety, keep reading this blog post as by the end of this article, you’ll be well on your way toward constructing a carbon steel grating built to last.
1. What is Carbon steel grating?
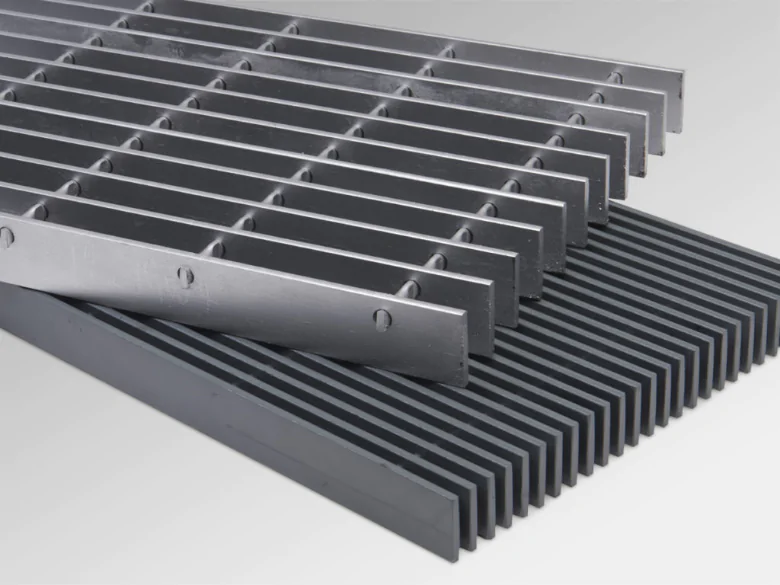
Carbon steel is a ubiquitous, economically beneficial material and incredibly durable. It is an iron-carbon alloy that contains varying amounts of carbon, usually ranging from 0.0218%-2.11%, with small additions of silicon, manganese, sulfur, and phosphorus for increased strength.
These properties make it ideal for use as the raw material of carbon steel gratings – making it an excellent choice for applications from infrastructure construction to building drainage channels.
Additionally, carbon steel offers many advantages over its rivals due to its capacity to be easily manipulated and improved upon at a fraction of the price. This has become increasingly relevant as major infrastructural projects are put into motion around the globe in the name of progress.
Two types of processing for welding
Hand welded
Hand-welded bar grating consists of deep rectangular cross bars and adjacent bearing bars that are connected by straight bearing bars. The deeper cross bar serving is welded together, while the top and bottom edges of the bearing bars are usually bolted together.
Hand-welded steel grating is created through pre-punched bearing bars, drilling of cross bars, and spot welding. This process allows for customization when complex types of gratings are needed; however, it is less intense than machine-press-welded steel grating.
An additional disadvantage is that gaps at contact points may sometimes need to meet customer requirements. Nevertheless, hand-welded steel grating plays an essential role in niche applications.
Machine press welded
Machine press welding process is an efficient process to produce metal gratings with a high degree of quality assurance. This method is preferred due to the speed at which it can be done, and as hydraulic resistance welding, an automatic pressure welding machine is used to join bearing bars and cross bars into one piece.
Furthermore, because of its dependability, it can be relied upon for mass production – saving money in the process due to its precision and accuracy compared with manual labor. The result is a steel grating structure with jointed stability and significant strength superiority.
2. Advantages of a carbon steel grating
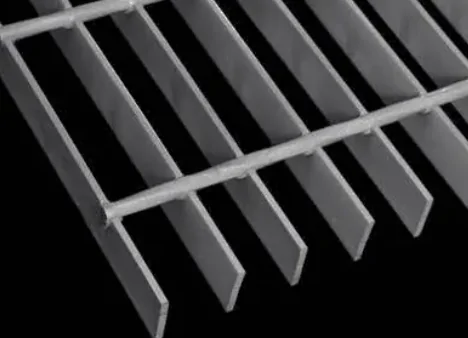
Carbon steel grating has a long history of use in industrial settings. They are an economical option for many applications, and their durability and strength make them an excellent choice for structures that will be exposed to heavy use.
With a standard plain surface and connecting bars, carbon steel grating is one of the easiest types of flooring to install. Hot dip galvanized carbon steel grating support an additional layer of protection against corrosion, which can be especially important in areas where moisture is an issue.
1 | Durability |
2 | Cost-Effective |
3 | Strength |
4 | Versatility |
5 | Fire Resistance |
6 | Aesthetics |
7 | Corrosion Resistance |
8 | Environmentally Friendly |
Durability
Carbon steel grating can last decades in extreme environments. This makes it ideal for outdoor and commercial applications exposed to harsh weather conditions, such as freezing temperatures or heavy rain.
Cost-Effective
Carbon steel grating is affordable compared to other materials, and suitable for projects on a tight budget. It also requires minimal maintenance, which helps reduce labor costs over the product’s lifespan.
Strength
Carbon steel grating offers superior strength and structural integrity, supporting heavier transferring loads and vehicular loads than other gratings. This makes it well-suited for industrial settings like industrial flooring where heavy machinery is used, and a high level of safety must be maintained at all times.
Versatility
Carbon steel grating can be manufactured into various shapes and sizes to fit applications. It can be welded together or cut into grating panels to serve as floor covering in warehouses, drain covers in driveways, or ventilation systems in factories and manufacturing plants.
Fire Resistance
Carbon steel grating offers excellent fire resistance properties due to its low thermal conductivity rating, making it a great choice for buildings that require extra fire safety precautions or work areas that involve flammable liquids or gases.
Aesthetics
Despite its industrial look and feel, carbon steel grating can still look attractive with the help of paint and powder coating options available today. These coatings help protect the metal from rusting while enhancing its appearance, making it suitable even in busy urban environments like parks or shopping malls where aesthetics are important considerations.
Corrosion Resistance
The surface of carbon steel grating is coated with anti-corrosion paints that afford additional protection against harsh chemicals and saltwater exposure common to many industrial flooring uses.
Environmentally Friendly
Recycled materials are often used during the production process of carbon steel grating which reduces energy consumption by up to 70% compared to other materials traditionally used in construction projects.
3. How to make a Carbon Steel Grating?
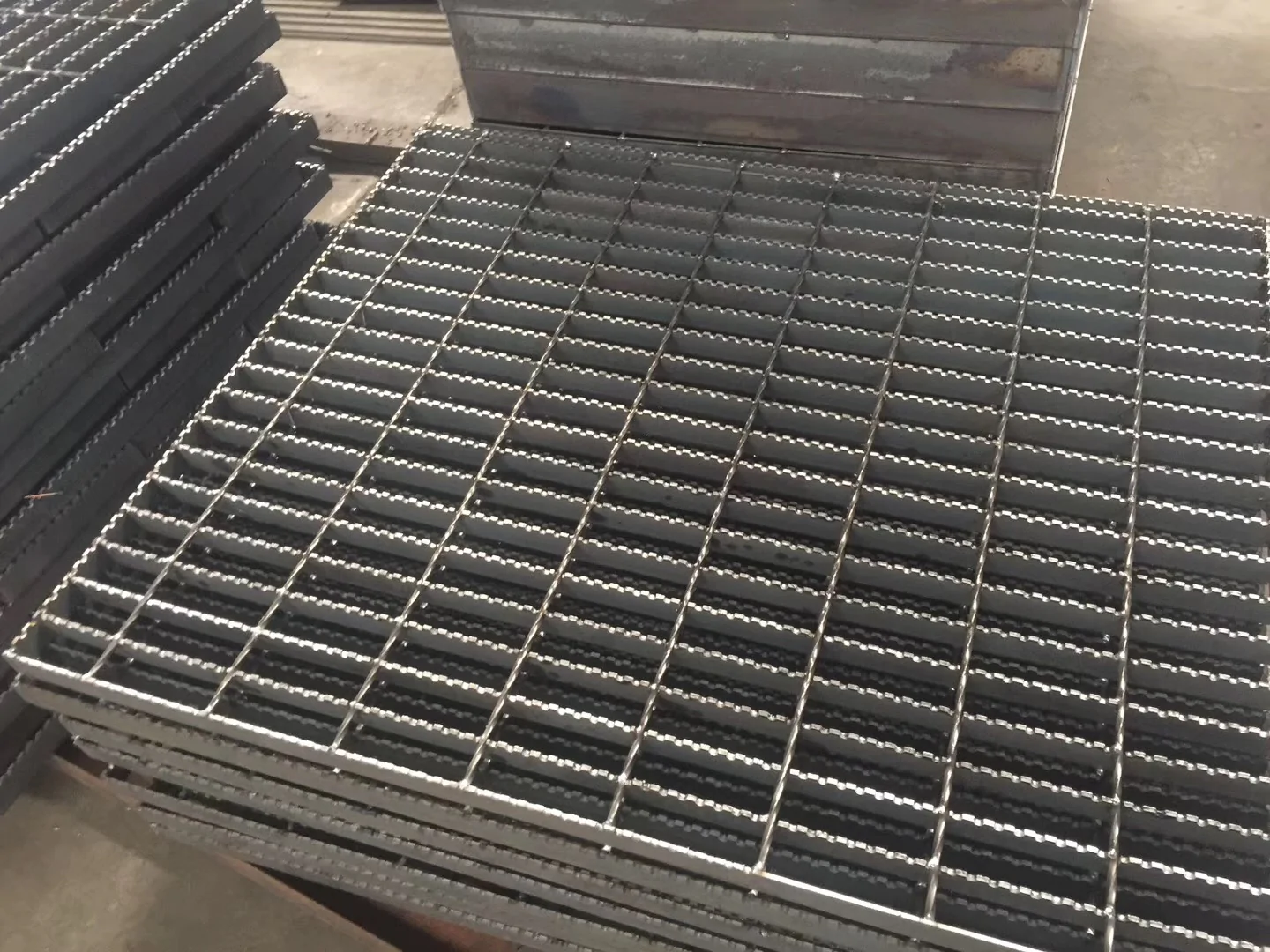
Step 1: Choose the Material
Carbon steel is ideal for producing gratings due to its corrosion resistance and strength. It is also economical, making it a popular choice for many applications. The material should be chosen based on the intended application, as different grades of carbon steel may be more suitable depending on the environment in which the grating will be used.
Step 2: Pressing/Welding
Then cut gratings to length and press or weld them together to form a solid grating panel that can withstand high levels of stress and pressure. When welding, care must be taken not to damage the integrity of the material.
Step 3: Cutting
After pressing/welding, the grating needs to be cut into sections that are easier to handle. This is done using either a guillotine or saw system, depending on the cutting required. Remember not to weaken any parts of the grating that could affect its strength and stability when installed.
Step 4: Banding
Once cut, banding can be applied around each section of the grating to secure it together when installed at its final location. Different banding types can be used depending on the installation type, such as stainless steel straps or specialty clips made from galvanized or stainless steel materials.
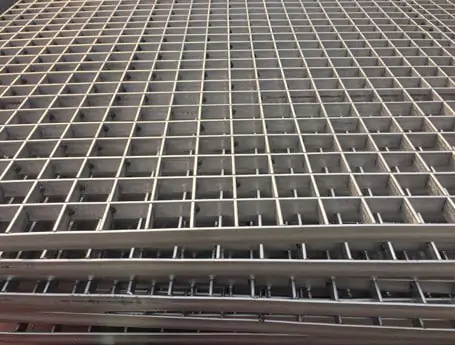
Step 5: Surface Treatment
Various treatments can be applied to ensure that your carbon steel grating look good and last long, such as painting, powdering and galvanizing, which helps protect against rust and oxidation while also improving aesthetics by adding color or texture differences. Also, hot dip galvanized is available for highly corrosive environments where regular coatings won’t suffice.
Step 6: Inspection
Before being shipped off for installation, each section should undergo rigorous testing and visual inspections to ensure quality control standards have been met throughout all manufacturing processes.
Quality assurance measures may include ensuring each bar has been appropriately welded and meets customer specifications, along with verifying dimensions are correct, and there are no signs of surface damage before shipping off the product for installation.
Step 7: Packaging
Once all tests have been passed, each section is carefully packaged with sturdy steel straps/ pallets, etc., to ensure it reaches its destination intact without any issues during transport.
4. Tips for manufacturing steel grating
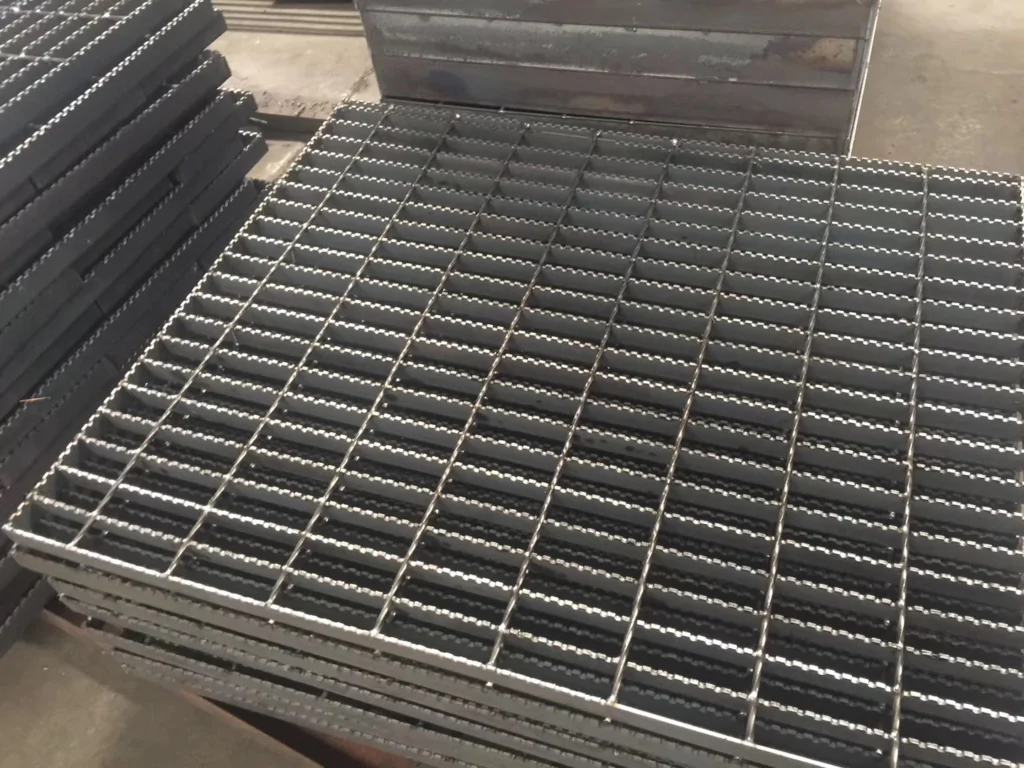
Check after surface treatment | After the treatment, sharp edges on the grating should be rounded off to prevent injuries. |
Installation | By bolting or welding, engineers could install the grating in place. And it is essential to use high-strength bolts that are appropriately sized for the load placed on gratings. |
Inspect and maintain | Clients should inspect it regularly for signs of damage or wear. Any damaged or worn parts should be repaired or replaced as soon as possible to prevent further damage or injury. |
5. What should clients consider during the process
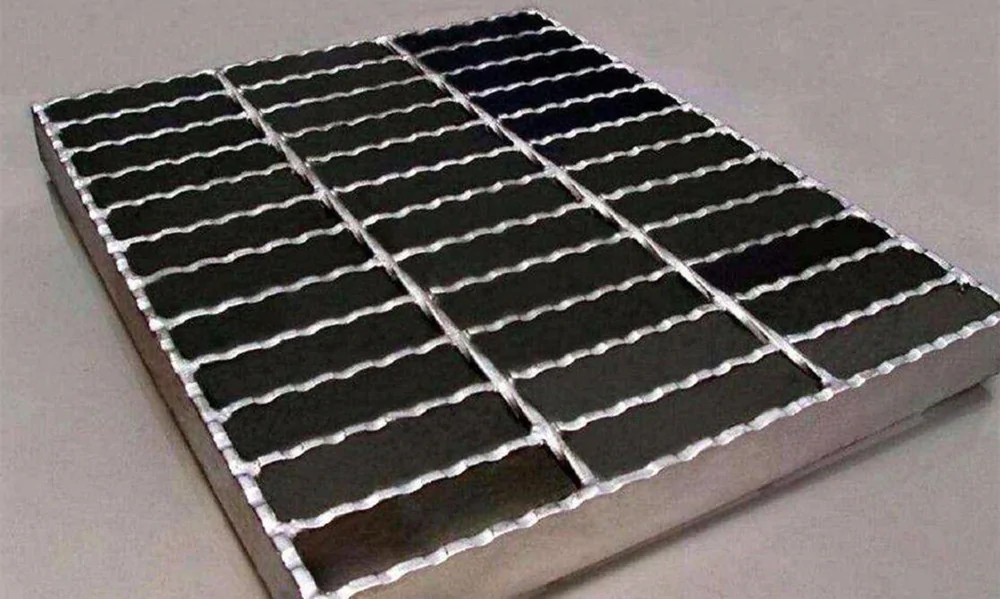
- The type of steel grating required
Three types of steel grating are welded steel grating, press-locked grating, and swage-locked grating. Each type has advantages and disadvantages that Clients should consider before making a decision.
- The size and shape of the grating
The size and shape of the grating will be determined by the application for which it is being used. For example, if the grating is to be used as a walkway, it will need to be large enough and have a specific shape to accommodate foot traffic.
- The load-bearing capacity
The client must consider the load-bearing capacity of the grating to ensure that it can support the weight of whatever will be placed on it. For example, if the grating is to be used as a platform in an industrial flooring setting, it will need to be able to support heavy machinery.
- The environment in which the grating will be used
Clients must also consider the environment in which the grating will be used. For example, if the grating is to be used outdoors, it must be made from weather-resistant materials.
Conclusion
When it comes to metals, carbon steel is one of the most affordable and versatile materials. This steel has a low carbon content, making it easy to work with different tools. It is cheap and rust-resistant, making it useful in many applications. Because of these properties, carbon steel is often used in construction projects involving thick bearing bars.
They are also used in various fields that need solid structural support. Following the tips above, you can create a custom metal grating that meets your needs.