In the industrial world, the decision to use steel or aluminum grating is often a pivotal one. Both materials have their distinct advantages and applications, making the choice far from straightforward. These unsung heroes play an instrumental role in countless operations, quietly contributing to safety, access, and drainage in an array of environments.
But how does one determine which grating material to use?
This comprehensive guide seeks to demystify the process, offering a head-to-head comparison of steel and aluminum grating and outlining the key factors to consider when choosing between them. Whether you’re an industry professional, a project manager, or just someone intrigued by industrial processes, read on to discover the fascinating world of grating.
Evaluating Steel Grating
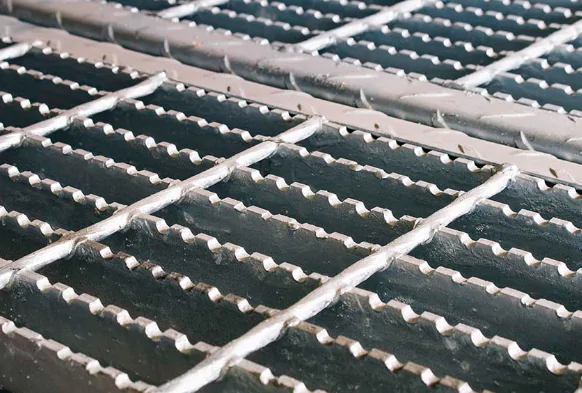
A. Description and Manufacturing Process of Steel Grating
Steel grating, a prevalent option for many industrial applications, comprises a series of bearing bars and cross rods. This interweaving network is typically made of high-strength, low-alloy steel.
The manufacturing process involves cutting and extending the steel reel, making them into the bars needed, and then placing them in the required pattern, welding it together using high heat or immense pressure, often through welding. The result is a robust, durable, and reliable grating solution.
B. Pros and Cons of Steel Grating
✅Pros | ❎Cons |
---|---|
Exceptional strength and durability; can withstand heavy loads and harsh conditions. | Quite heavy, which can complicate installation and transport. |
Suitable for high-traffic areas and heavy-duty applications. | More susceptible to corrosion unless treated appropriately. |
Can be galvanized to enhance resistance to corrosive elements, prolonging lifespan. |
C. Best Applications and Uses for Steel Grating
Industrial Walkways and Stairways: In industrial settings, steel grating is commonly used for walkways, catwalks, and stairways, providing safe, sturdy walking surfaces that allow light, liquid, and air to pass through.
Platforms: Steel grating is commonly used to construct raised platforms in industrial and manufacturing environments, warehouses, and other settings that require durable and reliable flooring.
Drainage Covers: Due to its ability to allow water to pass through while providing a sturdy surface for foot or vehicle traffic, steel grating is often used for drain covers and trench covers.
Bridges and Docks: Steel grating can be used in the construction of bridges and docks, providing a non-slip, durable surface.
Fencing and Partitions: In some applications, steel grating is used for fencing or partitions, offering security while allowing light and air to pass through.
Evaluating Aluminum Grating
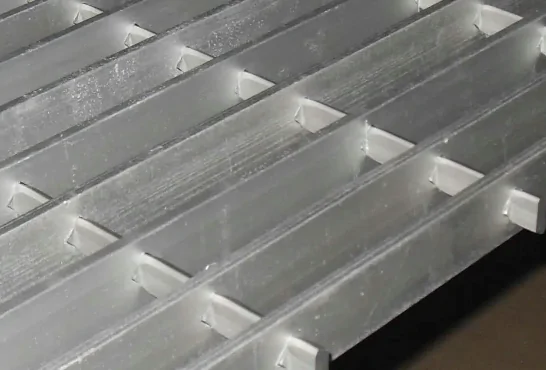
A. Description and Manufacturing Process of Aluminum Grating
Aluminum grating is a lightweight, durable material often used in industrial settings. It’s manufactured by a process known as pressure-locking or swaging, where cross rods and bearing bars made of aluminum are forcibly joined together. This forms a sturdy, interconnected network.
Due to the innate characteristics of aluminum, the finished grating is highly resistant to corrosion, making it ideal for environments exposed to water, chemicals, or harsh weather conditions. Furthermore, its lightweight nature significantly simplifies transportation and installation, thus adding to its practical advantages.
B. Pros and Cons of Aluminum Grating
✅Pros | ❎Cons |
---|---|
Stands out for its corrosion resistance and light weight. | Does not match the load-bearing capacity of steel grating. |
Easier to handle, transport, and install than steel grating. | Less suited for extremely heavy-duty applications. |
Resistant to weather conditions and maintains its aesthetic appearance over time. |
C. Best Applications and Uses for Aluminum Grating
Marine Environments: Aluminum grating is ideal for docks, piers, and boat lifts due to its natural resistance to saltwater corrosion.
Chemical Plants: Aluminum’s resistance to chemical corrosion makes its grating suitable for walkways, platforms, and drainage covers in chemical processing plants.
Wastewater Treatment Facilities: For similar reasons, aluminum grating is also used in wastewater treatment plants where corrosive substances are often present.
Food Processing Plants: Aluminum grating is used in food processing facilities because it’s easy to clean, corrosion-resistant, and non-toxic.
Architectural Applications: In architecture, aluminum grating is used for its aesthetic appeal and functional properties, such as sunscreens, building facades, ceilings, and decorative grilles.
Head-to-Head Comparison: Steel Grating vs Aluminum Grating
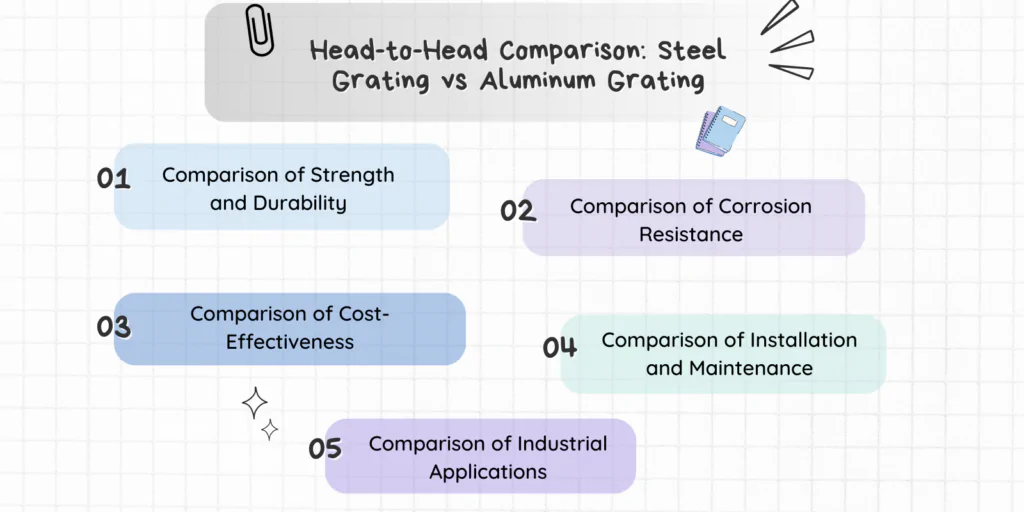
A. Comparison of Strength and Durability
Steel grating and aluminum grating are both robust choices, but they differ when it comes to strength and durability. Steel grating, built to withstand substantial weight and pressure, provides exceptional strength.
Its high load-bearing capacity makes it optimal for heavy-duty industrial applications like construction sites, power plants, or manufacturing units. Despite its lower weight, steel grating retains rigidity and doesn’t deform easily under pressure.
In contrast, while aluminum grating does offer considerable strength and durability, it doesn’t quite match up to steel in these respects. However, it’s important to note that for many applications, the strength of aluminum grating is more than sufficient. The unique swaging or press-locking process used in its manufacturing ensures a sturdy, interconnected network, making it resilient in handling moderate loads.
B. Comparison of Corrosion Resistance
Corrosion resistance is a vital consideration when choosing grating materials, and this is an area where aluminum grating shines. Aluminum naturally forms a protective oxide layer, making it highly resistant to corrosion. This makes it ideal for use in environments prone to moisture, harsh chemicals, or salty conditions, such as marine or chemical processing settings.
Steel grating, on the other hand, is more susceptible to corrosion. While treatments such as galvanization can enhance its resistance, making it suitable for many environments, untreated steel grating may corrode over time, especially in harsh environments. Therefore, even though treated steel grating can resist corrosion, it may not provide the same level of resistance as aluminum.
C. Comparison of Cost-Effectiveness
Steel grating | Less expensive initially, it may require more maintenance over time, particularly if it’s exposed to corrosive elements and not treated adequately |
Aluminum grating | Potentially more costly upfront, can provide cost benefits in the long run due to its corrosion resistance, and its lighter weight can lead to savings in transportation and installation costs |
D. Comparison of Installation and Maintenance
The weight of the grating material can significantly impact the ease of installation. Aluminum grating, being lighter than steel grating, is generally easier to handle, transport, and install, which can lead to labor and time savings.
In terms of maintenance, aluminum grating has the edge due to its natural corrosion resistance. While steel grating, particularly if galvanized, can resist corrosion to a certain degree, it may still require regular inspection and potential treatment to prevent rust and ensure longevity.
E. Comparison of Industrial Applications
Both steel and aluminum grating find wide usage across various industries, but their specific advantages make them better suited to certain environments. Steel grating, with its superior strength and durability, is ideal for heavy-duty industrial settings such as construction, manufacturing, and oil refineries.
On the other hand, aluminum grating, with its high corrosion resistance and lightweight nature, is preferred in corrosive environments, like chemical plants, wastewater treatment facilities, and marine applications. It’s also ideal for industries where weight is a key consideration, such as aerospace and transportation.
Factors to Consider When Choosing Between Them
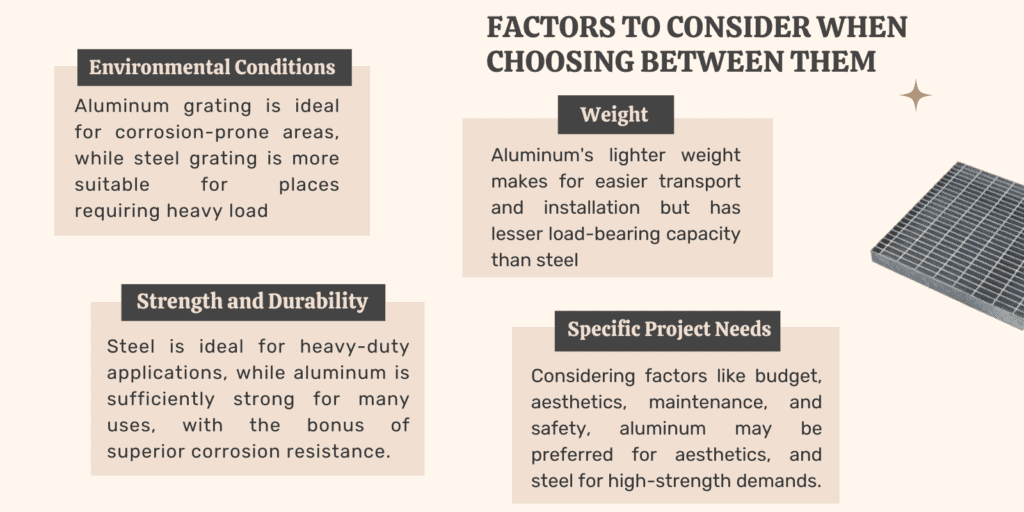
When choosing between steel and aluminum grating, a number of factors must be taken into consideration. These factors are not only important for the longevity and durability of the grating, but also for its cost-effectiveness, practicality, and suitability to the specific project requirements.
A. Environmental Conditions
The environment where the grating will be installed plays a crucial role in determining the best material. For instance, if the grating is to be used in a marine environment or a setting with frequent chemical exposure, corrosion resistance becomes paramount.
In such scenarios, aluminum grating, with its superior resistance to corrosion, would likely be the better choice. However, in environments where corrosion is less of a concern but high load-bearing capacity is needed, steel grating would be more suitable.
B. Weight
The weight of the grating can significantly impact both transportation and installation. Aluminum grating is lighter than steel grating, which makes it easier to transport and install, and could potentially lead to lower labor and logistical costs. However, it’s important to remember that the lighter weight of aluminum grating also translates to a lesser load-bearing capacity compared to steel.
C. Strength and Durability
The strength and durability requirements of your project are also important to consider. For heavy-duty applications requiring a high load-bearing capacity, steel grating is usually the superior choice due to its greater strength. However, aluminum grating can still offer ample strength for many applications and has the added advantage of superior corrosion resistance, which can contribute to its overall durability.
D. Specific Project Needs and Requirements
Finally, the specific needs and requirements of your project must be considered. This encompasses everything from budget constraints, design aesthetics, and maintenance requirements, to regulatory standards and safety concerns.
For example, in projects where aesthetics are important, the clean, modern look of aluminum might be preferred. Conversely, in settings where extreme strength is needed, such as in heavy manufacturing or construction sites, the robustness of steel grating would be more appropriate.
Conclusion
The decision between steel and aluminum grating is not one-size-fits-all. It requires a careful evaluation of various factors, including the intended application, environmental conditions, weight considerations, required strength and durability, and specific project needs.
While steel grating stands out in terms of strength and durability, aluminum grating shines for its corrosion resistance and light weight. By understanding the pros and cons of each, industry professionals can make an informed decision that best suits their specific requirements.